Waardestroomanalyse volgens Arend Oosterhoorn
Gepubliceerd in
Lean Six Sigma
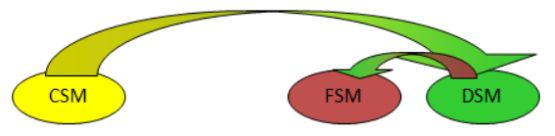
Arend Oosterhoorn definieert een waardestroomanalyse (WSA) als het beoordelen van een proces op zijn vermogen waarde te leveren: welke activiteiten vertegenwoordigen waarde en welke niet?
Binnen de Lean-filosofie is waarde die handeling of activiteit waar een klant voor wil betalen. Deze definitie geeft goed aan met welke mindset je kijkt naar de verschillende activiteiten in het proces, maar is niet in alle gevallen dekkend. Het gaat erom 'waarde' te bekijken vanuit het oogpunt van het doel van het proces, waarom het proces is ingericht, en wie uiteindelijk de 'betaler' is van de eindproducten van het proces. In die zin moet het begrip 'klant' breed worden gezien als ('wie betaalt, bepaalt').

Een organisatie bestaat uit een heleboel waardestroompjes; je kunt ieder proces op zich analyseren, of het nu om een maakproces of om een beleidsproces gaat. Ieder proces is ingericht om iets op te leveren voor iemand die er iets mee gaat doen en waarvoor de uitkomst van het proces dus waarde vertegenwoordigt.
In essentie is de (totale) waardestroom het geheel van handelingen en activiteiten dat start bij het verkrijgen van de order of de opdracht en eindigt bij de aflevering van het product.
Een waardestroomanalyse heeft als doel de verspillingen vast te stellen, door voor activiteiten vast te stellen of het gaat om toegevoegde waardeactiviteiten of niet-toegevoegde waardeactiviteiten.
Het proces van waardestroomanalyse omvat drie stappen:
-
Opstellen Current State Map: in kaart brengen van de huidige situatie.
-
Dream State Map: op basis van de inventarisatie van de huidige situatie en de ongemakkelijkheden die daaruit naar voren komen, vaststellen van hoe het proces - zonder beperkingen tussen droom en daad - idealiter zou verlopen, oftewel: de 'gedroomde status' (Dream State)'.
-
Future State Map: bepalen van de op korte termijn realiseerbare verbeterde situatie, zolang droomstatus (nog) niet haalbaar is.
Bron: Waardestroomanalyse, Arend Oosterhoorn
Laatst aangepast op woensdag, 19 augustus 2020 15:04
Value Stream Mapping volgens Arend Oosterhoorn
Gepubliceerd in
Lean Six Sigma
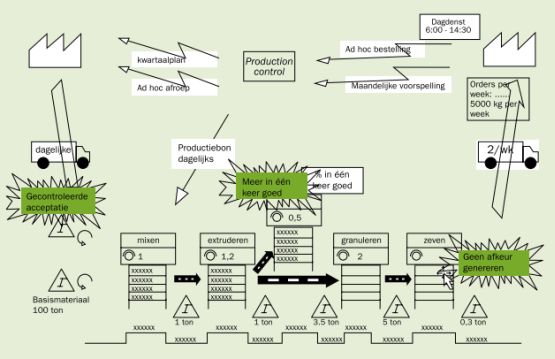
In het artikel Value Stream Mapping beschrijft Arend Oosterhoorn de Value Stream Map, hét instrument om binnen de flow van zowel materiaal als de informatie duidelijk te visualiseren.

Het doel van de Value Stream Map (VSM) is inzicht te krijgen in de totale flow van het materiaal via de verschillende bewerkingsstappen, in combinatie met de informatie die deze materiaalstroom aanstuurt. Daar wordt een tijdlijn aan gekoppeld om te zien hoeveel tijd er daadwerkelijk wordt besteed aan het toevoegen van waarde, en hoeveel wachttijd er in het proces zit, wat geen waarde toevoegt.
[Een] Value Stream Map [maak je in een aantal stappen]:
1. Teken de klant, de leverancier en de Production Control boven in de map. 2. Geef aan wat de afnamebehoefte van de klant is (per dag/week/...). 3. Bepaal wat de dagelijkse productiecapaciteit is. 4. Teken het transportsymbool voor de verzending van expeditie; geef daarbij ook aan wat de frequentie van de leveringen is. 5. Teken de transportsymbolen voor de aanlevering van de grondstoffen; geef daarbij ook de frequentie aan (als er meerdere zijn met verschillende frequenties, geef dat weer in een tabelletje). 6. Teken nu alle processymbolen conform de stappen in het proces in de juiste volgorde, van links naar rechts. 7. Voeg daar de databoxen aan toe. 8. Teken nu de communicatielijnen van klant naar Production Control, van Production Control naar leveranciers en van Production Control naar het proces. Geef daarbij ook de frequentie aan. 9. Vul de databoxen met relevante informatie op basis van metingen. Zoals capaciteit, up-time, omsteltijden, storingstijden en dergelijke. 10. Teken de operatorsymbolen in het proces daar waar operators staan en geef aan om hoeveel operators het gaat. 11. Voeg de voorraadlocaties toe en geef omvang en verblijfduur aan. 12. Beschrijf de stroom door gebruik te maken van de push- en pull-tekens. 13. Maak nu onderaan de tijdlijn, met added value time en non-added value time. 14. Voeg ook de werktijden toe van de fabriek. 15. Tenslotte is het mogelijk om aan te geven waar verbetering mogelijk is door felgekleurde Kaizensymbolen op de uiteindelijke VSM te plakken.
[Het maken van een VSM] is een uitgebreid proces wat veel waardevolle informatie oplevert, vooral omdat het een totaalbeeld geeft. Dat totaalbeeld van de huidige situatie noemen we de Current State Map.
Dream State Map Wil je nu verbeteren, start dan met de Dream State Map, doe alsof je helemaal opnieuw kunt beginnen zonder beperkingen, hoe zou de situatie er dan uit zien? Dit levert vaak heel interessante inzichten op.
Future State Map Als je terugkeert op aarde en bedenkt dat toch niet alles onbeperkt mogelijk is, dan kun je vanuit deze Dream State Map de Future State Map maken, de beschrijving van de haalbare verbetering. Die bevat dan meer verbeteringen dan wanneer je vanuit de Current State Map gaat werken.
Laatst aangepast op zaterdag, 14 juli 2018 15:57
Six sigma volgens Marcel van Assen
Gepubliceerd in
Lean Six Sigma
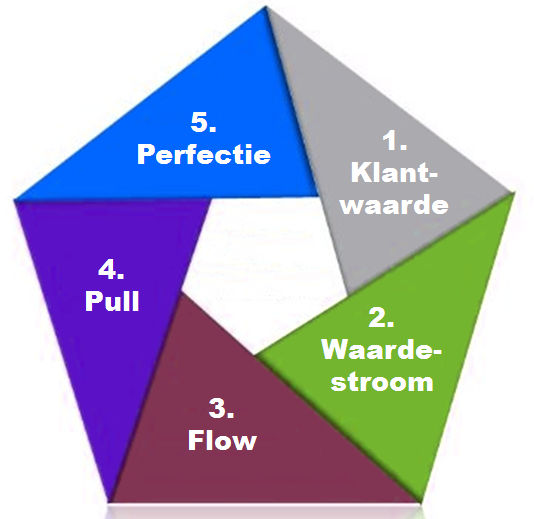

Lean kent een standaard-verbeterproces dat begint met het in kaart brengen van doelstelling(en). In het algemeen komt dat neer op het bepalen wat klanten (van het bedrijfsproces) precies willen, ofwel wat klantwaarde is. Het op het juiste moment precies maken en leveren van de juiste producten en diensten (die klantwaarde opleveren) staat centraal binnen Lean. Het proces dat continu klantwaarde moet opleveren, wordt daarom 'waardestroom' genoemd.
[Binnen het ontwerp- en verbeterproces zijn er] vijf essentiële stappen om een slanke waardestroom met de juiste besturing te krijgen:
(1) Value
1.1 Definieer wat klantwaarde is en daarmee wat de klant als verspilling ziet.
1.2 Bepaal de procesdoelstellingen (KPI-targets)
(2) Valuestream
2.1 Ontwikkel een VSM met de verschillende processtappen en analyseer waar waarde wordt gecreëerd.
(3) Flow
3.1 Bepaal welke activiteiten waarde toevoegen of welke cruciaal zijn voor de bedrijfsfunctie.
3.2 Verwijder alle niet-waardetoevoegende activiteiten die niet van cruciaal belang zijn voor de bedrijfsfunctie.
(4) Pull
4.1 Stroomlijn het primaire proces zodanig dat de vraag gebalanceerd is met de capaciteit
4.2 Zorg dat de lijn stroomt met vaste takttijd
4.3 Bestuur de lijn met pull-besturingssysteem zoals een kanban- of two-binsysteem
(5) Perfection
5.1 Borg de verbeteringen
5.2 Perfectioneer de organisatie middels Kaizen-workshops
5.3 Creëer een cultuur van continu verbeteren
Ad (1) Value (bepaal klantwaarde)
Onderzoek de eisen en wensen van klanten en bepaal wat de klantwaarde precies is. Door nauwkeurig te analyseren wat van waarde is voor de klant, leert de organisatie ook wat de klant als verspilling zal beschouwen. Dit is het uitgangspunt voor het analyseren en optimaliseren van de waardestroom.
Ad (2) Value stream (bepaal de waardestroom)
Waarde wordt aan klanten geleverd via de waardestroom, die in het ideale geval geen enkele niet-waardetoevoegende activiteit bevat. In deze stap wordt per productfamilie een zogenaamde value-stream map ontwikkeld van de huidige situatie. Onderzoek vervolgens welke activiteiten wel/geen waarde toevoegen.
Ad (3) Flow (zorg dat de activiteiten doorstromen)
Zorg voor een lopendebandachtige productie: maak dat goederen en diensten door de processen heen stromen via het elimineren van de niet-waardetoevoegende activiteiten en andere vormen van verspilling. In de Lean-filosofie zijn wachtrijen, batchproductie en transport belangrijke hindernissen bij het bereiken van productieflow, omdat deze buffers de doorlooptijd (vanaf het moment dat de productie aanvangt tot de oplevering ervan) verlengen. In deze stap zorgt men ervoor dat de processen zodanig zijn geoptimaliseerd dat het werk zo mogelijk zonder besturing door het proces heen stroomt. Zorg daarbij voor orde en netheid, bijvoorbeeld door het toepassen van de 5S-methode.
Ad (4) Pull (laat de klant de producten of diensten door het proces trekken)
Synchroniseer de productie met de werkelijke vraag van de klant. Producten en diensten moeten door het proces heen worden getrokken op basis van de werkelijke vraag van de klant. De waardestroom moet reactief worden gemaakt om het product of de dienst alleen te leveren als de klant het nodig heeft, niet eerder of later. De besturing is verder niet groter of complexer dan strikt noodzakelijk. De bekendste pull-besturingsmethoden zijn het two-bin-systeem en het kanbansysteem.
Ad (5) Perfection & prevention (optimaliseer het proces voortdurend)
Streef naar perfectie door processen voortdurend te verbeteren met behulp van Kaizen-events/bursts of Kaizen-blitzes.
Bron: Handboek Lean management - aanpak, concepten en modellen voor het succesvol toepassen van Lean, Marcel van Assen
Laatst aangepast op zaterdag, 14 juli 2018 15:56
Procesmatrix volgens Neil Webers, Lucas van Engelen & Thom Luijben
Gepubliceerd in
Lean Six Sigma
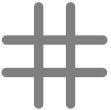
Neil Webers, Lucas van Engelen & Thom Luijben beschrijven in hun boek Het groot verbeterboek - meer dan 120 tools en concepten voor procesverbeteraars en verandermanagers het Analyse-instrument van de procesmatrix:

De procesmatrix is een overzicht van alle factoren die mogelijk invloed hebben op een prestatie-indicator. Per invloedsfactor wordt aangegeven of het een stuurvariabele, ruisvariabele of een verstoring is, en of het verwachte effect op de te verbeteren prestatie-indicatoren sterk, beperkt of nihil is.
De procesmatrix is in wezen een rapportage. Deze geeft deelnemers aan een verbeterproject de gelegenheid om te zien of invloedsfactoren die zij hebben genoemd ook worden gerapporteerd. ... De classificatie in stuurvariabelen, ruisvariabelen en verstoringen wordt later gebruikt om de verbetermaatregel af te stemmen op de variabele in kwestie. De inschatting van het effect op de prestatie-indicatoren is een hulpmiddel om een selectie te maken van factoren die nader onderzocht moeten worden om de meest cruciale te vinden.
Aanpak
Stap-1
[Maak een tabel] met in de eerste kolom het proces dat wordt bekeken, in de tweede kolom de potentiële invloedsfactor, in de derde kolom de typering van de invloedfactor, in de vierde kolom de effectinschatting op de prestatie-indicator en in de vijfde kolom ruimte voor opmerkingen.
Stap-2
Schrijf alle verzamelde invloedsfactoren op in de tweede kolom. Deze invloedsfactoren zijn de opbrengst van de verschillende methoden zijn de opbrengst van de verschillende methoden voor het benoemen en opsporen van invloedsfactoren, zoals brainstormen, interviews met experts en Best-of-Best (BoB)-analyse versus Worst-of-Worst (WoW)-analyse.
Stap-3
Bepaal van elke factor of het een ruisvariabele is (een factor die continu aanwezig is in het proces, maar niet te manipuleren), een stuurvariabele is (een factor die wel te manipuleren is) of een verstoring is (een incidenteel voorkomende factor die het proces verstoort) en zet dit in kolom 3.
Stap-4
Geef van elke potentiële invloedsfactor het effect op de prestatie-indicator weer. Noteer dit met ++ als er een groot effect is, met + als er een beperkt effect is en een 0 als er niet of nauwelijks een effect is.
Stap-5
Geef in kolom 5 de relevante opmerkingen en met name de bewijsvoering (indien aanwezig) voor de effectinschatting uit kolom 4.
De procesmatrix wordt opgeleverd aan het einde van de Analyse-fase (A) van het DMAIC-stappenplan.
Bron: Het groot verbeterboek - meer dan 120 tools en concepten voor procesverbeteraars en verandermanagers, Neil Webers, Lucas van Engelen & Thom Luijben
Laatst aangepast op woensdag, 19 augustus 2020 15:08
Hoshin Kanri volgens Marcel van Assen
Gepubliceerd in
Lean Six Sigma
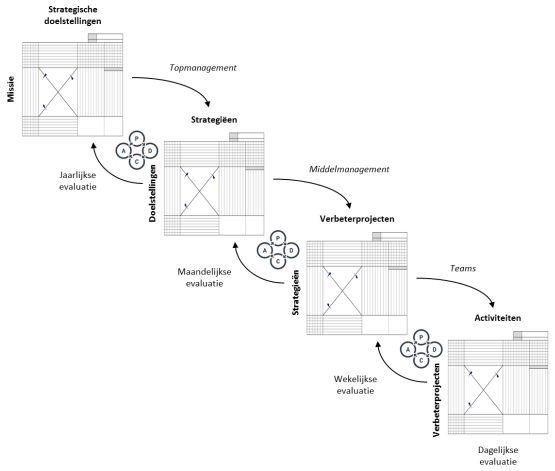
Marcel van Assen stelt in zijn boek Handboek Lean management dat Hoshin Kanri in feite neerkomt op een cascade van PDCA-cycli:

Vrij vertaald betekent Hoshin de 'methode om strategische richting te geven' terwijl 'Kanri' management betekent. Hoshin Kanri staat voor het management(proces) van beleidsontwikkeling en strategie-implementatie, ook wel policy deployment genoemd.
(...)
Via Hoshin Kanri worden de missie, visie en strategische doelstellingen van de organisatie opgesteld door het topmanagement in een eerste PDCA-cyclus. Bovendien worden KPI's vastgesteld waarmee gemeten kan worden in hoeverre de strategische doelstellingen worden gerealiseerd, passend bij de (veranderende) organisatie-omgeving. Vervolgens vindt er in de lagere organisatieniveaus een cascade van PDCA-cycli plaats, waarbij de uitkomsten van de PDCA-cyclus op de hoger gelegen managementlaag de input zijn vor de PDCA-cyclus op het organisatieniveau daaronder.
(...)
In ieder geval wordt er aldus voor gezorgd dat iedereen heel goed op de hoogte is van de strategische doelen, zodat iedereen dezelfde kant uit werkt. De bedoeling van Hoshin Kanri is ook dat iedereen in de organisatie zich bewust is van de kritieke succesfactoren van de organisatie (CSF’en) en de daarop gebaseerde prestatie-indicatoren (KPI’s), en dat afdelingen elkaar niet tegenwerken door miscommunicatie en slecht afgestemde afdelingsplannen. Ook zijn op deze wijze alle verbeterprojecten op elkaar afgestemd en zijn ze consistent met de ambities en doelstellingen van de organisatie.
(...)
Visie en richting alleen is niet voldoende. Het gaat om de doorvertaling van de missie en visie in concrete richtinggevende doelstellingen, die weer door het niveau daaronder worden gebracht om de juiste tactische (verbeter)projecten en processen te ontwikkelen op basis waarvan individuele en operationele (verbeter)acties geïnitieerd kunnen worden. De strategische richting, de Hoshin, vormt een leidraad voor alle acties op alle organisatieniveaus. Dit zorgt ervoor dat verbeteractiviteiten gecoördineerd kunnen worden en dat iedereen in dezelfde richting werkt.
(...)
Een Hoshin-Kanri-matrix (de X-matrix) laat zien welke doelen, welke projecten, welke maatregelen (oplossingen) en hun resultaten gelden op een bepaald gebied en/of en bepaald organisatieniveau, en wie verantwoordelijk is voor het realiseren van de gestelde doelen. De Hoshin Kanri-matrix is een vast onderdeel van de informatieborden in een werkcel, lean-war room en/of mini-company.
(...)
Hoshin Kanri biedt de mogelijkheid om continu prestaties te meten, te evalueren, te verbeteren en de resultaten ervan te verspreiden in de organisatie, zodat iedereen ongeacht functie op de hoogte is van de visie, richting, doelstellingen en plannen van de organisatie, en iedereen dus in dezelfde richting werkt en verbetert. Omdat er een top-down focus wordt geëist en er hooguit vier of vijf doelstellingen gedefinieerd mogen worden, wordt ervoor gezorgd dat er niet te veel verbeterprojecten en –acties in de organisatie gestart worden.
De uitgangspunten van Hoshin Kanri zijn: - Meet het bedrijfssysteem als geheel - De hoofddoelstelling van het bedrijf als geheel is bekend - Inzicht in de omgeving waarin het bedrijf actief is, is essentieel - De processen en activiteiten inclusief de doelstellingen en prestatie-indicatoren ervan zijn bekend - Er worden voldoende middelen beschikbaar gesteld om de noodzakelijke activiteiten uit te voeren en zo de bedrijfsdoelstellingen te bereiken.
Beleidsuitvoering (Hoshin Kanri) is enerzijds een top-down-methode, om te kunnen sturen op resultaat en anderzijds staat het creëren van consesus (Nemawashi) centraal vanwege dialoog en reflectie aangaande de doelen, het bespreken van de voortgang en de gerealiseerde prestaties, en het gezamenlijk beslissen over eventuele maatregelen (bijsturen). Dit gebeurt in een bottom-up-beslisproces dat ‘Ringi’ wordt genoemd.
Een Hoshin Kanri is niet alleen een top-down-cascade van PDCA-cycli, maar ook een bottom-up-beslisproces middels Ringi-sho.
Een van de voordelen van Hoshin Kanri is dat het de medewerkers in verschillende lagen helpt om niet alleen te horen te krijgen wat ze moeten doen en hoe ze dat moeten doen, maar vooral waarom. Hoshin Kanri is de methode om inspirerend en visionair leiderschap te tonen door richting te geven en focus aan te brengen. Hoshin Kanri kent immers een eenduidige gerichtheid op enkele belangrijke doelen. Via Hoshin Kanri wordt een gedeeld beeld gecreëerd van de toekomst, een soort ‘Ware Noorden’ (True North) als einddoel dat richting geeft en waaraan de tactiek – oftewel de route om het Ware Noorden te bereiken – gekoppeld kan worden.
Bron: Handboek Lean management - aanpak, concepten en modellen voor het succesvol toepassen van Lean, Marcel van Assen
Bewaren
Laatst aangepast op zaterdag, 14 juli 2018 15:20
Continu verbeteren met Marcel van Assen
Gepubliceerd in
Lean Six Sigma
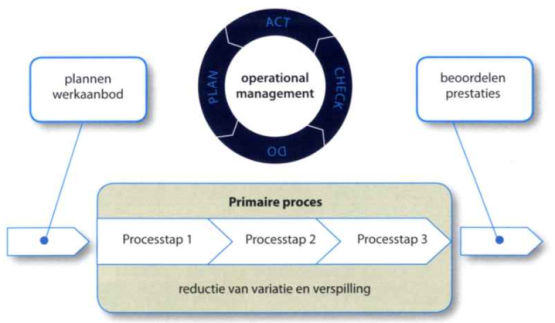
In het artikel Operational excellence verlangt continu verbeteren beschrijven Joes Wigma, Roel Notermans en Marcel van Assen hoe het sturen op de operatie en continu verbeteren met elkaar verbonden zijn op basis van een (vereenvoudigd) procesmodel:
Het beheersen van een proces kan door input, proces en output te meten. Meten aan de inputzijde maakt vroegtijdig ingrijpen mogelijk wanneer zich afwijkingen ten opzichte van de gestelde norm voordoen. Dit heet ook wel feed forward. Door real time te meten, kan bij afwijkingen ten opzichte van de gestelde norm nog tijdens het proces worden bijgestuurd. Tot slot kan door meten achteraf gecheckt worden of aan de gestelde doelen is voldaan. Dit heet ook wel feed back.
Vertaalslag Hierna volgend de belangrijkste elementen van operationeel management.
-
Operationele doelen. Vanuit de strategische doelen moet een organisatie de vertaalslag maken naar de operationele doelen voor het betreffende proces. Deze doelen zijn vertaald in meetbare indicatoren (Key Performance Indicators, KPI's) die helder zijn voor en beïnvloedbaar zijn door de betrokkenen in het proces. ... Probeer maximaal 5 tot 7 KPI's te definiëren en werk aan de verbetering van niet meer dan een of twee tegelijk.
-
Vooraf en achteraf meten. Het meten van de input van een proces is een belangrijk en vaak sterk onderschat deel van de operationeel managementcyclus. Zo kan een organisatie tijdig bijsturen om de uiteindelijke klant op tijd goede kwaliteit te leveren. Aan inputzijde moet in ieder geval de hoeveelheid werk (werkvoorraad) en de kwaliteit van het aangeleverde materiaal gemeten worden. Daarnaast moet een organisatie beoordelen in hoeverre zij gestelde doelen ook realiseert. Deze informatie vormt de belangrijkste input voor de verbetercyclus (...).
-
Plan-do-check-act (verbeteren langs de Deming-cirkel). De vergelijking tussen doel en realisatie is in feite het uitvoeren van de plan-do-check-act-cyclus. Veel bedrijven doorlopen deze cyclus wel, maar lang niet alle geven ook gevolg aan de uitkomsten van de evaluatie in een actieplan. En juist deze laatste stap - als organisatie bepalen welke verbeteringen doorgevoerd moetn worden om de doelen wel te halen - is zo belangrijk; in de literatuur ook veel besproken aan de hand van kaizen events (Japans voor 'veranderen naar beter' of 'verbetering'). (...).
[Volgens Wigma, Notermans en Van Assen zijn er drie soorten bijeenkomsten nodig voor het vertalen van de methodiek van operationeel management naar de praktijk]. Twee voor het sturen op de operatie (dagoverleg en weekoverleg) en een derde voor het uitwerken van mogelijke verbeteringen (verbeterbijeenkomsten).
Het dagoverleg is gericht op het bijsturen van het operationele proces en het inventariseren van kleine direct uitvoerbare verbeteringen. Het weekoverleg is bedoeld voor het identificeren van mogelijke grotere verbeteringen aan de hand van evaluatie van KPI's. Zowel het dag- als het weekoverleg is gericht op het realiseren van operationele doelen. Het is van belang dat de teamleider en medewerkers deze doelen begrijpen, kunnen beïnvloeden en dat hun prestaties op deze doelen zichtbaar zijn. Hiervoor gebruikt men veelal een glass wall op een voor de afdeling centrale plek. Deze glass wall bevat de KPI's, maar ook zaken als een skill matrix (wie kan wat op welk niveau), een opleidingsplan en verbeteracties met verantwoordelijke, datum ingediend en datum gereed. Bovendien is zo'n glass wall te gebruiken voor het presenteren van de afdelingsresultaten aan andere geïnteresseerden en versterkt deze de betrokkenheid en het teamgevoel.
Verbeterbijeenkomsten zijn bedoeld om mogelijke verbeteringen ook uit te werken en in te voeren. Alle verbetervoorstellen moeten gericht zijn op een verbetering van doelen (KPI's) die op het wandbord staan en besproken worden in het weekoverleg.
Bron: Operational excellence verlangt continu verbeteren, Joes Wigma, Roel Notermans en Marcel van Assen; in: In INL, nummer 4/5 - 2008
Laatst aangepast op zaterdag, 14 juli 2018 15:19
Stroomdiagram volgens Arend Oosterhoorn
Gepubliceerd in
Lean Six Sigma
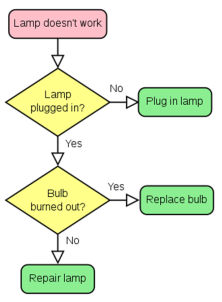
In het boek 111 instrumenten voor kwaliteitsverbetering - Ingedeeld volgens de Six Sigma-verbetercyclus beschrijft Arend Oosterhoorn het instrument van het stroomdiagram:

Doel
Het stroomdiagram is een instrument voor het helder weergeven van het verloop van een proces.
Werking
Door via grafische symbolen de stroom van activiteiten in een proces weer te geven, wordt een helder beeld verkregen van het verloop van een proces. Daarbij wordt gebruik gemaakt van gestandaardiseerde symbolen.
- Terminal: symboliseert het begin en het einde van het proces.
- Proces: geeft de activiteiten in het proces weer. In dit symbool staat dus altijd een werkwoord.
- Beslissing: bevat dus altijd een vraag. Afhankelijk van het antwoord, dat meestal op de uitgaande lijnen wordt weergegeven, gaat het proces verder.
- Input/output: geeft aan wat het proces binnenkomt en wat het proces verlaat. In de meeste gevallen start een proces als er een document of een product binnenkomt, dus na het startsymbool volgt meestal een input/output-symbool.
- Parameter: lijst van te controleren parameters bij bijvoorbeeld controles in het proces.
- Document: aangegeven wordt welk document in een proces wordt gebruikt (bijv. een werkinstructie) of welk document het proces verlaat (bijv. een offerte). De richting van de pijlen geeft aan of het document wordt gebruikt (van het documentsymbool naar het processymbool) of dat het document in het proces wordt gegenereerd (van het processymbool naar het documentsymbool).
(...)
Aanpak
(1) Bepaal welk proces in kaart moet worden gebracht.
(2) Bepaal de grenzen van het proces; alles wat het proces in komt is invoer, alles wat het proces verlaat is uitvoer.
(3) Start het tekenen van het stroomdiagram met het terminalsymbool met daarin de tekst 'start'.
(4) Teken daar rechtsonder het input/output-symbool waarin wordt aangegeven wat het proces binnenkomt en als 'trigger' werkt om het proces te starten.
(5) Teken nu de eerste activiteit in het processymbool, verbind dit via een lijn met het startsymbool en teken de lijn vanaf het input/output-symbool naar deze lijn.
(6) Volg nu de activiteiten en beslissingen binnen het proces alsof je er een film van maakt. De activiteiten worden beschreven met het processymbool, en de omschrijving bevat dus altijd een werkwoord; de beslissingen worden beschreven met het beslissymbool en bevatten dus (vrijwel) altijd een vraag.
(7) Documenten die worden gebruikt bij een processtap, worden met het document-symbool aangegeven met een pijl in de richting van het processymbool; documenten die door de activiteit worden gegenereerd, worden weergegeven met een documentsymbool met een pijl, gericht van het processymbool af.
(8) Als een activiteit een controle betreft, kan in het parametersymbool worden aangegeven welke kenmerken er allemaal moeten worden gecontroleerd.
(9) Beëindig alle stromen die het proces verlaten met een terminalsymbool met de tekst 'stop'. Dat kunnen er meerdere zijn omdat een proces verscheidene mogelijkheden kan hebben om te stoppen (waar dan ander processen doorgaan).
Bron: 111 instrumenten voor kwaliteitsverbetering - Ingedeeld volgens de Six Sigma-verbetercyclus, Arend Oosterhoorn
Laatst aangepast op maandag, 28 september 2020 15:45
Critical-to-Quality (CTQ) volgens Marcel van Assen
Gepubliceerd in
Lean Six Sigma
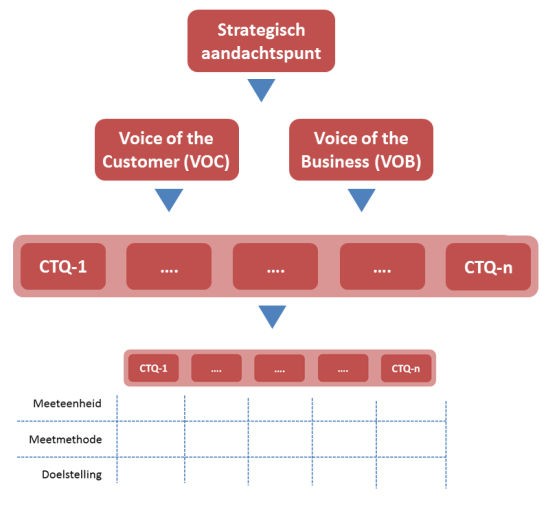
Volgens Marcel van Assen leidt een Voice-of-the-Customer-analyse (of een Kano-analyse) tot een overzicht met klantenwensen en -eisen, ofwel de functionaliteiten die klanten willen hebben.

"Een belangrijk onderdeel in [Lean] is het in kaart brengen van de klanteneisen en -wensen, namelijk de voice-of-the-customer. De VOC, ofwel de stem van de klant, is de vertaling van de eisen, wensen en verwachtingen die klanten hebben aangaande de producten en diensten van de organisatie. Hiervoor worden gegevens verzameld (bijvoorbeeld klachtenbrieven, enquêteresultaten, opmerkingen, en uitkomsten van marktonderzoek en interviews) die de standpunten en/of behoeften van klanten vertegenwoordigen. Deze gegevens moeten worden vertaald (operationeel gedefinieerd) naar een of meer gekwantificeerde eisen voor een product of dienst (en de daarbij behorende processen). ... Hetzelfde wordt gedaan bij stakeholders. Deze eisen worden vertaald in een voice-of-the-business (VOB).
(...)
De VOC of VOB heeft altijd en relatie met de strategie van de organisatie. Het heeft geen zin om klanteisen en -wensen te analyseren van klanten uit product/markt-combinaties die geen onderdeel zijn van de bedrijfsstrategie. De VOC's/VOB's die er wel toe doen, worden vertaald in en of meer CTQ's (afkorting van Critical-to-Quality) via een VOC/VOB-CTQ-boom (CTQ-flowdown).
Een CTQ (ook wel genoemd 'cruciaal voor kwaliteit') is een geoperationaliseerd kenmerk van een product of dienst, noodzakelijk voor de prestatie, betrouwbaarheid of maakbaarheid van dat product of die dienst, en daarmee voor de klanttevredenheid.
Om te kunnen onderzoeken of alle CTQ's voldoen aan de gestelde normen, wordt eerst voor elke CTQ vastgesteld wat de meeteenheid, de meetmethode en de te behalen doelstellingen zijn.
Bron: Handboek Lean management - aanpak, concepten en modellen voor het succesvol toepassen van Lean, Marcel van Assen
Bewaren
Laatst aangepast op zaterdag, 14 juli 2018 15:19
Six sigma volgens Marcel van Assen
Gepubliceerd in
Lean Six Sigma
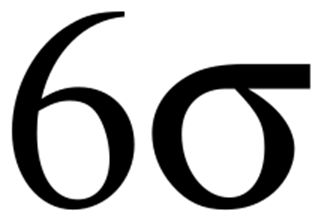
Six Sigma is een kwaliteitsverbetermethode die officieel in 1985 is ontwikkeld door Bill Smith (vice president en senior quality assurance manager bij Motorola) om systematisch processen te verbeteren door defecten te elimineren. Hoewel Smith de methodologie in belangrijke mate zelf heeft ontwikkeld, is zijn werk vooral gebaseerd op vele jaren onderzoek op het gebied van kwaliteitsverbetering en bouwt het voort op het werk van Juran, Feigenbaum, Crosby, Deming, Ishikawa en Imai).
Al vanaf de jaren twintig tot aan de jaren tachtig van de vorige eeuw is er door verschillende auteurs veel geschreven over kwaliteitsmanagement (en in hetbijzonder over Total Quality Control en Total Quality Management). Tegenwoordig wordt kwaliteitsmanagement (TQM) vooral gezien als een gestructureerde methode voor het continu verbeteren van bedrijfsprocessen.
De grondlegger van TQM is Joseph Juran, die al in het begin van de jaren vijftig van de vorige eeuw een boek had geschreven over kwaliteitsmanagement in organisaties (Juran, 1951). Hierin benadrukte hij dat het menselijke aspect bij kwaliteitsmanagement. Ook Armand Feigenbaum (hoofd operations General Electric) benadrukte dat kwaliteit de verantwoordelijkheid is van iedereen binnen een organisatie, dus zowel van het management als van het personeel. Daarnaast legde Feigenbaum nadruk op het financiële aspect van kwaliteitsverbeteringen — bij het selecteren van de beste verbeterprojecten moeten de project en die de hoogste ROI leveren als eerste worden uitgevoerd (Feigenbaum, 1961). Daarmee heeft Feigenbaum (net als Philip Crosby) een belangrijke bijdrage geleverd aan de kwaliteitskostentheorie (Costs of Quality). Ook Philip Crosby, die de zero defect methode introduceerde (Crosby, 1979), stelde dat kwaliteit vooral gemeten moest worden aan de hand van de kwaliteitskosten, maar de methode om kwaliteit te verbeteren is volgens hem vooral voorkomen dat de vereiste normen niet worden gehaald.
William Edwards Deming was het niet helemaal met Philip Crosby eens en vond juist dat kwaliteit gemeten zou moeten worden door middel van statistische analyse. Volgens Deming zijn alle bedrijfsprocessen onderhevig aan variatie waardoor de kwaliteit van processen kan worden verbeterd door juist deze variatiete verminderen. Een belangrijke bijdrage van Deming aan kwaliteitsmanagement is zijn Plan-Do-Check-Act cirkel, wat uiteindelijk de aanpak voor continue verbeteren is geworden. Ook Deming benadrukt het belang van de betrokkenheid van de gehele organisatie in verbeterprocessen. Daarvoor dienen alle medewerkers te worden getraind in kwaliteitstechnieken en statistische methoden, uiteraard met het oog op het terugdringen van procesvariatie. In de huidige Six Sigma methode zijn veel onderdelen van de aanpak van Deming opgenomen, waarvan de belangrijkste ‘het meetbaar maken van kwaliteit door middel van statistische analyse’ is (Deming, 1982). Juran borduurde daarop voort en kwam in 1988 met zijn befaamde boek Juran on Planning for Quality waarin hij opperde om vooral de process capability van processen te analyseren en op basis daarvan de minder goede processen te verbeteren (ook dit is één van de belangrijkste onderdelen van de huidige Six Sigma methodologie). Bovenden gaf Juran een verbeteraanpak die sterk lijkt op de verbeteraanpak van Six Sigma (Juran, 1988: p15)
Naast deze Amerikaanse auteurs zijn ook enkele Japanse auteurs van invloed geweest op Six Sigma, vooral Kaoru Ishikawa en Masaaki Imai. Ishikawa is de kwaliteitsgoeroe die de oorzaak-en-gevolg diagram (root-cause-analysis) heeft bedacht; één van de pijlers van Six Sigma. Verder vertaalde en integreerde Ishikawa de ideeën van Deming en Juran in de Japanse industrie en legde de nadruk op het zo eenvoudig mogelijk maken van continu verbeteren door gebruik te maken van kleine verbeterteams. Masaaki Imai is echter de ‘grondlegger’ van continu verbeteren (Kaizen) met de befaamde boeken Kaizen: The key to Japan’s competitive success (1986) en Gemba Kaizen: A commonsense, low-cost approach to management (1997).
Waar Total Quality Management zich vooral richt op het continu verbeteren en het steeds verder optimaliseren van hetzelfde proces, is Six Sigma vooral gericht op het uitvoeren van één of meer ‘eindige’ projecten die per stuk het doel hebben om een forse verbetering (van de procesbetrouwbaarheid) te realiseren in een bepaald proces. De process capability is het centrale begrip waarmee de betrouwbaarheid van een bedrijfsproces wordt weergegeven (wat staat voor de procesvariatie in relatie tot de gespecificeerde norm). De process capability wordt gebruikt om de variatiebronnen van deelprocessen op te sporen en te verwijderen. Met andere woorden, binnen de Six Sigma-filosofie wordt de probleemoplossing primair gestuurd in de richting van variatiereductie en besparingen wat ervoor zorgt dat processen niet onnodig worden herontworpen als dat niet strikt noodzakelijk is.
Six Sigma omvat enkele sleutelconcepten, waaronder:
-
Critical to quality (CTQ): attributen die het meest belangrijk zijn voor de klant. Klanttevredenheid is één van de centrale thema’s binnen Six Sigma.
-
Defects (fouten): dit zijn alle oorzaken waardoor niet geleverd wordt wat de klant wenst (dat wil zeggen de oorzaken van non-conformance aan de CTQ).
-
Process capability: een maat voor wat een proces kan afleveren.
-
Root cause analysis: een methode (of groep van probleemoplossende methoden) gericht op het vaststellen van de echte oorzaken van een probleem (of gebeurtenissen). Het is gebaseerd op het Ishikawa-diagram (ook wel visgraat- of oorzaak-gevolgdiagram genoemd), vernoemd naar de bedenker Kaoru Ishikawa.
Bron: Handboek Lean management - aanpak, concepten en modellen voor het succesvol toepassen van Lean, Marcel van Assen
Laatst aangepast op zaterdag, 14 juli 2018 18:46
Training Within Industry (TWI) volgens Schultz, Heuveling & Vlerken
Gepubliceerd in
Lean Six Sigma
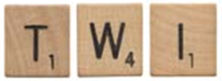

Tijdens de Tweede Wereldoorlog vochten de Amerikaanse mannen aan het front en bleven de vrouwen achter. Deze achtergebleven vrouwen werden aangemoedigd om in de fabrieken, waar wapentuig werd geproduceerd, te gaan werken. "Rosie de Riveter" stond model voor deze gemotiveerde, hardwerkende vrouwen. Haar slogan was: "We can do it."
De vrouwen en andere ongetrainde arbeiders, maakten daarbij gebruik van werkstandaarden en protocollen en werden daarbij geholpen voor een Amerikaans programma dat "Training Within Industry" (TWI) werd genoemd. Dit programma, ontwikkeld in opdracht van de Amerikaanse overheid, bestond uit een trianing op de werkvloer, verbetering van werkmethoden, onder andere standaardisatie en een andere manier van leidinggeven.
Na de Tweede Wereldoorlog raakte dit TWI-programma in Amerika wat in de vergetelheid, maar in Japan werd het des te meer gewaardeerd tijdens de wederopbouw. TWI lag mede aan de basi van de ontwikkeling van het Toyota Productie Systeem en dus ook van het Lean werken.
Bron: Lean in de huisartsenpraktijk - een introductie in het implementeren van Lean in de praktijk, Ulrich Schultz, Margareth Heuveling & Maud van Vlerken
Laatst aangepast op donderdag, 21 juni 2018 21:06
|