Doorlooptijdanalyse volgens Gerrit-Jan Obers & Ko Achterberg
Gepubliceerd in
Lean Six Sigma
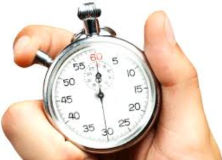
In het boek Grip Bron: Grip op processen in organisaties beschrijven Gerrit-Jan Obers & Ko Achterberg hoe je de doorlooptijd van een proces kunt analyseren. Obers en Achterberg beschouwen de doorlooptijdanalyse één van de technieken voor het kwantitatief analyseren van processen. Doorlooptijdanalyse is een (meet)instrument voor het onderzoeken van de eigenschappen van een bedrijfsproces. De doorlooptijd is de tijd die nodig is voor de afhandeling van een (klant)vraag in een procesketen of werkproces. Het gaat dus om de tijd die nodig is om de vraag het proces geheel te laten doorlopen.
Volgens Obers en Achterberg is niet alleen de doorlooptijd zelf van belang bij de analyse van de doorlooptijd, maar ook hoeveel de doorlooptijd verbeterd kan worden. Een maatstaf hiervoor is de doorlooptijdefficiëntie, die aangeeft hoeveel de gemeten doorlooptijd afwijkt van de minimale doorlooptijd.

Direct bepalen van de gemiddelde doorlooptijd (T)
De doorlooptijd is de hoeveelheid tijd die één stroomeenheid (één aanvraag, dienst of product c.q. één geval) doorbrengt binnen het proces.
Van belang is vast te stellen wat er door het proces stroomt, de stroomeenheid. Wat stroomt er precies door het voortbrengingsproces? Bijvoorbeeld in een restaurant kun je de klant beschouwen als stroomeenheid, maar je kunt ook de menuorder van de klant als stroomeenheid zien. Bij een paspoortaanvraag kun je de burger als stroomeenheid zien, maar je kunt ook het paspoort als stroomeenheid beschouwen. De stroomeenheid kan zijn een eenheid input, een eenheid output, een set inputs of een set outputs, tussenproducten enzovoort. (...)
Sommige aanvragen of dienste bewegen zich zonder wachttijden, zonder vertraging door een proces, andere brengen wellicht lange tijd in het proces door in afwachting van het beschikbaar komen van de benodigde capaciteit. De doorlooptijd kan van geval tot geval aanzienlijk verschillen. Daarom gaan we uit van een gemiddelde doorlooptijd (T). Dat wil zeggen, we nemen het gemiddelde aan doorlooptijden van een aantal geleverde producten of diensten die gedurende een specifieke tijdsperiode door het proces bewegen.
De gemiddelde doorlooptijd (T) van een gegeven proces kunnen we direct vaststellen in de volgende stappen:
-
Stel de te meten stroomeenheid vast en stel vast wat je beschouwt als beginpunt en eindpunt van het proces (of de procesketen).
-
Observeer het proces over een gespecificeerde tijdsperiode.
-
Neem steeksproefsgewijs enkele stroomeenheden die in de gespecificeerde periode door het proces bewegen. Om een statisch verantwoord beeld te krijgen, moet je dit voor een relevant aantal gevallen doen. In de statistiek spreekt men dan over 'steekproef', 'steekproefomvang' en 'populatie'.
-
Meet de doorlooptijd voor elke geselecteerde stroomeenheid van begin tot einde van het proces.
-
Bereken de gemiddelde doorlooptijd van de gemeten stroomeenheden.
Indien je gegevens vastlegt over de gebeurtenissen (events) aan het begin (start-event) en het einde van het proces (eind-event), dan kun je ook zonder feitelijke waarneming van het proces de gemiddelde doorlooptijd berekenen. Hiervoor moeten de gegevens van het start- en eind-event minimaal zijn aan te wijzen aan hetzelfde geval (case) én het betreffende tijdstip (time-stamp) bevatten. Maar het is wel verstandig ook met directe waarneming in het proces vast te stellen of de vastlegging in het systeem overeenkomt met de werkelijkheid. Denk bijvoorbeeld aan een stapel aanvragen op papier die nog in het systeem moeten worden ingevoerd.
Indien aan deze voorwaarden voldaan is, dan kun je de berekening op deze gegevens baseren, wat kan leiden tot een nauwkeuriger beeld van de doorlooptijd. Hieraan kun je vervolgens een analyse koppelen omtrent de typen die een langere of kortere doorlooptijd hebben.
Bepalen van de doorstroomsnelheid (Sn)
De doorstroomsnelheid is het gemiddelde aantal stroomeenheden (aanvragen, diensten of producten c.q. gevallen) dat door het proces stroomt in een gegeven tijdsinterval. De procescapaciteit is de maximaal ondersteunde doorstroomsnelheid.
Doorstroomsnelheid en procescapaciteit zijn belangrijke factoren van procesprestatie. Hoe hoger de doorstroomsnelheid, hoe hoger het rendement van een proces is. Capaciteit is belangrijk omdat onvoldoende capaciteit kan leiden tot buitensporige wachttijden en daarmee een lange doorlooptijd.
De gemiddelde doorloopsnelheid (Sn) van een proces kun je als volgt vaststellen:
-
Identificeer het beginpunt en eindpunt van een proces.
-
Stel het tijdsinterval vast (uur, dag, week) waarover je wilt meten.
-
Meet het aantal diensten dat gedurende het gedefinieerde tijdsinterval de geïdentificeerde begin- en eindpunten passeert.
-
Herhaal dit voor enkele andere tijdsintervallen.
-
Bereken het gemiddelde aantal stroomeenheden (Sn) dat per gekozen tijdsinterval door het proces stroomt.
Indien de doorstroomsnelheid voor verschillende tijdsintervallen sterk varieert, is sprake van een grote doorstroomveranderlijkheid. Deze kan veroorzaakt worden door variatie in het werkaanbod en de factoren binnen het proces, bijvoorbeeld onjuiste planning, storingen, ziekte, enzovoort.
De doorstroomsnelheid wordt bepaald door de capaciteit van een proces. Een proces kent een theoretische capaciteit en een werkelijke capaciteit. De theoretische capaciteit wordt zelden benut als gevolg van interne inefficiënties in het proces die leiden tot niet-beschikbaarheid van resources en stilstand. Zo ontstaat een bezettingsgraad van een proces die wordt bepaald door de doorstroomsnelheid en de theoretische capaciteit (bezettingsgraad = doorstroomsnelheid / theoretische capaciteit).
Deze bezettingsgraad is een belangrijke indicator voor de mate waarin voorzieningen (machines, mensen) worden benut. Voorzieningen betekenen geïnvesteerd kapitaal en kosten. De voortgebrachte producten en diensten leveren omzet en winst op. De bezettingsgraad beïnvloedt zo het rendement van de organisatie. De uitdaging is om ook bij grote variaties in het werkaanbod en een hoge bezettingsgraad de doorlooptijden te beheersen.
Indirect bepalen van de doorlooptijd
Het direct bepalen van de doorlooptijd door waarneming of gebruik van event-gegevens kan een kostbare of tijdrovende aangelegenheid zijn, zeker bij lange doorlooptijden en het ontbreken van gegevens. Daarom ligt het voor de hand om te zoeken naar een eenvoudiger techniek voor het bepalen van de doorlooptijd. Dt kan dor het indirect bepalen van de gemiddelde doorlooptijd (T) met behulp van de hiervoor behandelde doorloopsnelheid (Sn) en de hoeveelheid onderhanden stroomeenheden binnen de procesgrenzen op een specifiek tijdstip. Dit laatste noemen we het aantal onderhanden zijnde stroomeenheden (Se).
De relatie tussen deze grootheden is dat het aantal onderhanden zijnde stroomeenheden (Se) gelijk is aan de gemiddelde doorloopsnelheid x de gemiddelde doorlooptijd.
Dat betekent dat je de gemiddelde doorlooptijd T kunt berekenen door het aantal onderhanden stroomeenheden (Se) te delen door de gemiddelde doorstroomsnelheid (Sn). In veel gevallen kun je op deze manier de doorlooptijd in een korte periode bepalen, ook indien deze veel langere tijd duurt.
Met de relatie tussen deze grootheden (Se = Sn xT) kun je vanzelfsprekend ook andere berekeningen maken. Indien de doorlooptijd en de doorstroomsnelheid bekend zijn, dan kun je de gemiddelde hoeveelheid onderhanden werk berekenen.
(...)
Doorlooptijdefficiëntie
De doorlooptijd geeft aan aan hoe lang een organisatie bezig is geweest met de behandeling. Maar de doorlooptijd geeft niet aan hoeveel uren (tijd) de organisatie heeft besteed aan de inhoudelijke behandeling of uitvoering van het (primaire) proces; dit noemen we de bewerkingstijd. De totale bewerkingstijd is de som van de uren (tijdsduur) die medewerkers of machines nodig hebben om de activiteiten uit te voeren. De doorlooptijd zal in de praktijk vaak (veel) groter zijn dan de totale bewerkingstijd. Om allerlei redenen van structurele of incidentele aard kan het zijn dat werk blijft liggen tot het aan de beurt is. Er zijn vele factoren die vertragingen veroorzaken in het behandeltraject.
Deze factoren zorgen ervoor dat de doorlooptijd groter is dan de bewerkingstijd. Een van de principes van Lean Thinking is dat het verschil tussen doorlooptijd en de totale bewerkingstijd zo klein mogelijk gemaakt moet worden om de kans op verspilling te minimaliseren. Een maatstaf hiervoor is de doorlooptijdeffiiciëntie.
Om inzicht te krijgen in de efficiëntie van de doorlooptijd kun je de gemiddeld gerealiseerde doorlooptijd vergelijken met de theoretisch haalbare doorlooptijd. In formulevorm is dit als volgt weer te geven:
Doorlooptijdefficiëntie = theoretische doorlooptijd / gemiddelde doorlooptijd.
De theoretische doorlooptijd wordt bepaald door de bewerkingstijd van de activiteiten (en eventuele transporttijd) op het kritieke pad van activiteiten, dat wil zeggen de langste keten van met elkaar samenhangende activiteiten.
(...)
De doorlooptijdanalyse geeft aan hoe lang een organisatie bezig is geweest met de behandeling. Maar deze doorlooptijd geeft niet aan hoeveel uren (tijd) de organisatie heeft besteed aan de inhoudelijke behandeling of uitvoering van het (primaire) proces (bewerkingstijd) of hoeveel tijd een opdracht helemaal niet werd behandeld maar lag te wachten (wachttijd). Soms is ook sprake van tijd voor transport tussen de activiteiten (transporttijd).
De totale doorlooptijd is dan ook de som van alle afzonderlijke wachttijden, bewerkingstijden en evt. transporttijden.
Bewerkingstijd
Tijd die nodig is om het inhoudelijke werk uit te voeren, als mens en voorzieningen gereed zijn om direct aan de uitvoering te beginnen. Als de uitvoering niet wordt verstoord door de telefoon, de loop naar het koffieapparaat, conversatie met een collega en dergelijke, noemen we de bestede tijd de netto bewerkingstijd. Het opruimen van gebruikte spullen hoort overigens ook tot de bewerkingstijd. In een volledig geautomatiseerd proces kan de bewerkingstijd in de orde van grootte van milliseconden tot enkele seconden liggen. Bij een volledige handmatige uitvoering, met veel onderzoekswerk, kan de duur variëren van minuten tot uren of zelfs dagen.
Wanneer we bij het bepalen van de bewerkingstijd uitgaan van vastgelegde gegevens (start- en eindtijd), vinden we meestal de bruto bewerkingstijd. Met behulp van (fysieke) waarnemingen kunnen we verstoringen zien en kan de netto bewerkingstijd worden vastgesteld.
Transporttijd
Tijd die nodig is om het werk en de werkopdracht van de ene werkplaats naar de andere te verplaatsen. Bij transport kun je denken aan verplaatsing van fysieke goederen in een productieomgeving, bijvoorbeeld vervoer van sinaasappelen van de veiling naar een winkelier. Maar ook de bezorgtijd van een brief door de postbode en electronische verzending van gegevens valllen hieronder, bijvoorbeeld e-mail of gestructureerde berichten. Bij electronisch transport kan sprake zijn van buffering van berichten of van beperkingen in de beschikbaarheid van systemen. Dit betekent dat het transport vaak deels bestaat uit wachten en deels uit daadwerkelijk transport.
Wachttijd
Tijd tussen het moment dat een klant of geval of zaak zich aandient en het moment waarop de klantbediening of gevalsbehandeling start. Wachttijd kan optreden bij het allereerste begin, als de behandeling of bediening nog moet starten. Ook gedurende het gehele proces kan wachttijd ontstaan. (...) Vanuit het perspectief van een organisatie is wachttijd op te vatten als de tijd waarin het werk ligt te wachten op de (vervolg)behandeling.
(...)
[Wachttijden] kunnen een aanzienlijk deel van de doorlooptijd vormen. Het komt regelmatig voor dat de behandeling van een geval in totaal wellicht slechts enkele tientallen minuten bewerkingstijd kost, terwijl de doorlooptijd soms oploopt tot vele weken of zelfs enkele maanden wegens de vele (vormen van) wachttijd. Wachttijd kan een doorslaggevende factor vormen in de totale doorlooptijd. Hier moet je niet blind op afgaan. Het is nodig zicht te krijgen op de grootte van de tijdscomponenten die de doorlooptijd bepalen. De meeste winst is meestal te behalen door je te richten op de grootste bijdragen op de doorlooptijd.
Bron: Grip op processen in organisaties, Gerrit-Jan Obers & Ko Achterberg
Laatst aangepast op woensdag, 26 augustus 2020 18:36
Dagstarts volgens Bert Teeuwen (2)
Gepubliceerd in
Lean Six Sigma
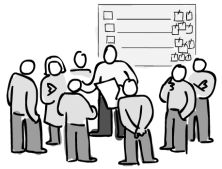
Bert Teeuwen beschrijft in Dagstarts en Hoshin Kanri - Continu Leren en Verbeteren in de juiste richting met Dagstarts en Hoshin Kanri de praktische spelregels van de dagstart:

Dagstarts hebben orde en regelmaat nodig om de kwaliteit ervan te borgen. Een dagstart moet een routine met vaste regels worden, en routines ontstaan pas na gedisciplineerd oefenen en inslijten. Dagstarts met steeds wisselende begintijden en open agenda's krijgen nooit de kans om een routine te worden. Neem als je een dagstart gaat ontwerpen ook de tijd om met de teamleden de regels van orde vast te stellen.
Denk daarbij aan het volgende:
- Start altijd exact op tijd.
- Iedereen heeft zich goed voorbereid.
- Een dagstart duurt nooit langer dan 15 minuten.
- Hanteer een vaste agenda.
- De dagstart is niet om uitvoerig te discussiëren.
- Rond elk agendapunt af door kort samen te vatten.
- Voer de prestatiedialoog aan de hand van een vaste set van coachingsvragen.
- Verbetervoorstellen zijn alleen akkoord als ze een bijdrage levren aan de (team-)doelstellingen.
- Van dagstarts worden geen verslagen of notulen gemaakt. Alles is vastgelegd op een overzichtelijk dagstartbord. Iemand die de dagstart gemist heeft, kan de resultaten van het gesprek en de actiepunten op dat bord vinden.
- Iedereen is er. Dagstarts stimuleren het collectieve leren en verbeteren.
Een ander type regels gaan over de omgangsvormen. De manier waarop men elkaar respectvol aanspreekt en naar elkaar luistert.
Zoals:
Wij
- Vallen elkaar niet in de rede.
- Luisteren naar elkaar met als doel de ander te begrijpen.
- Hebben respect voor elkaars bijdrage.
- Discussiëren alleen over een onderwerp als we de feiten kennen.
- Willen continu collectief leren en verbeteren en helpen elkaar daarbij.
- Delen onze kennis en standaarden.
Bron: Dagstarts en Hoshin Kanri - Continu Leren en Verbeteren in de juiste richting met Dagstarts en Hoshin Kanri, Bert Teeuwen
Laatst aangepast op maandag, 28 januari 2019 20:34
Hoshin Kanri volgens Bert Teeuwen (2)
Gepubliceerd in
Lean Six Sigma
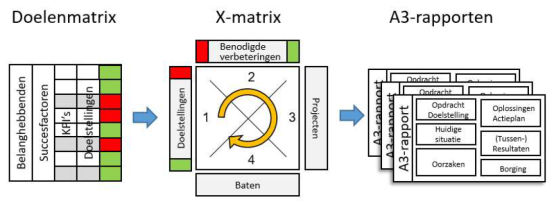
Bert Teeuwen beschrijft in Dagstarts en Hoshin Kanri - Continu Leren en Verbeteren in de juiste richting met Dagstarts en Hoshin Kanri hoe je binnen een organisatie met Hoshin Kanri alle neuzen dezelfde kant op krijgt:

In de doelenmatrix staan de verbeterdoelen, gelinkt aan de succesfactoren van de verschillende belanghebbenden. In de X-matrix zijn die gekoppeld aan de benodigde inspanningen. De A3-rapporten bevatten de gedetailleerde projectbeschrijvingen. De doelstelling van een project komt rechtstreeks uit de X-matrix. Het is de mix van de 'benodigde verbetering' en de 'baten' die met kruisjes aan het project gelinkt zijn. De voortdurende bijgewerkte A3-rapporten dienen als verslagvan de voortgang van de projecten.
Cascaderen met X-matrices
Doelen van afdelingen en die van de organisatie als totaal moeten met elkaar samenhangen. Hoe mooi zou het zijn als de doelen op alle niveaus met elkaar een oorzaak-gevolg-relatie hebben. Nog mooier is het als ook de geplande verbeter-inspanningen een plaats hebben in dat oorzaak-gevolg-plaatje. Een cascade van doelen en inspanningen, waarbij elk project niet alleen is terug te herleiden wat die moet gaan opbrengen. Maar ook aan welke afdelingsdoelstelling het een bijdrage zal leveren, en hoe dat ervoor zorgt dat het halen van de organisatie-doelstellingen een stapje dichterbij komt. En, als klap op de vuurpijl, dat het aantoonbaar een zetje in de juiste richting is, namelijk die van de strategische meerjarendoelen.
De Hoshin Kanri-methodiek met doelenmatrices, X-matrices en A3-rapporten werkt als volgt:
(1) Bepaal aan de hand van een strategische visie of een paar strategische doelen de doelenmatrix voor de hele organisatie. Laat daarin de stem van de klanten doorklinken. Bespreek deze met de managers van de afdelingen of waardestromen.
(2) De managers van de afdelingen of waardestromen maken met hun team van leidinggevenden een doelenmatrix voor hun niveau.
(3) Beoordeel met de strategische X-matrix of deze afdelingensdoelenmatrices een sluitend geheel vormen met elkaar en met de bovenliggende doelenmatrix. Pas aan waar dat nodig is.
(4) Bepaal op afdelingsniveau of op waardestroom-niveau welke obstakels en verliezen aangepakt moeten orden (de benodigde verbeteringen) om de doelen te gaan halen. Zet die in de X-matrix, en vul die verder in.
(5) Bepaal aan welk project welke benodigde verbetering gaat realiseren. Beoordeel hoeveel tijd en geld al die projecten gaan kosten. Ga, als blijkt dat het allemaal te veel is, weer onderhandelen. En pas de doelenmatrices aan op het resultaat van dat gesprek.
(6) Werk, als er consensus over de doelenmatrices en de X-matrices is, de gekozen projecten verder uit in A3-rapporten.
(7) Ontwerp de dag- en weekstarts op de diverse niveaus, zodat die met elkaar een cascade van informatie vormen om het verbeteren in de organisatie te volgen en te sturen. De directie volgt en bestuurt het strategische proces in zijn eigen strategische weekstart.
(...)
Het Catchball-proces
Hoshin Kanri is co-creatie. Iemand zei eens: "Hoshin Kanri helpt ons om de neuzen dezelfde richting op te krijgen, dat we allemaal hetzelfde lied zingen." De methodiek om in co-creatie de strategie te maken heet Catchball. Dat woord is in het Hoshin Kanri-proces de metafoor voor het horizontaal en verticaal naar elkaar overgooien van de bal - de deelresultaten -, die vangen, bestuderen en verder uitwerken en verbeteren. Die deelresultaten zijn dan het visiedocument, de doelenmatrices en de X-matrices. Het vangende team reageert op wat ze krijgt. niet met de rode pen, maar in gesprekken tussen werpers en vangers. Daarbij gebruik makend van de kennis en ervaring die ze hebben van de Stem van de Klant en de Stem van het Proces.
Bron: Dagstarts en Hoshin Kanri - Continu Leren en Verbeteren in de juiste richting met Dagstarts en Hoshin Kanri, Bert Teeuwen
Laatst aangepast op donderdag, 26 oktober 2017 06:00
Continu verbeteren volgens Kaizen
Gepubliceerd in
Lean Six Sigma
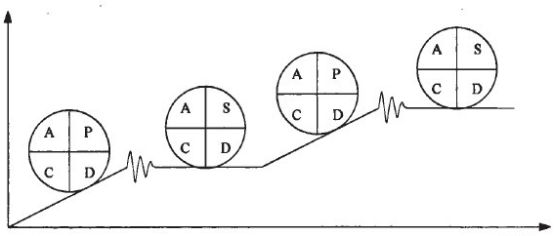

'Kaizen' (letterlijk in het Japans: "Ky'zen" = verbetering) wil in een brede betekenis zeggen:
"Voortdurende verbetering waar iedereen bij betrokken is: topmanagement, middenkader en uitvoerenden"
(...)
"In Japan behoort verandering tot het gewone leven. Volgens de Kaizen-filosofie verdient onze manier van leven - op ons werk, ons sociale leven of ons leven thuis - het om voortdurend te worden verbeterd" (Imai)
(...)
Geleidelijke verbetering in plaats van schoksgewijs
Imai onderscheidt twee soorten veranderingen: geleidelijke en revolutionaire veranderingen. Terwijl beide soorten in Japan voorkomen, maken geleidelijke veranderingen (welke nu juist kenmerkend zijn voor Kaizen) niet zo'n duidelijk deel uit van de Westerse manier van leven. Naast het handhaven van de bestaande toestand en het doorvoeren van ingrijpende wijzigingen door innovatie, legt men in Japan sterke nadruk op het tussenliggende gebied: de voortdurende inspanning om (kleine) verbeteringen door te voeren. Hierbij heeft elk hiërarchisch niveau zijn taak.
Continu verbeteren volgens Kaizen
De activiteiten die nodig zijn voor het in gang zetten van verbeteringen en het vastleggen van verbeteringen in nieuwe normen en standaarden volgen een patroon dat vergelijkbaar is met het zogenaamde 'Deming-wiel'.
Verbeteren volgens de PDCA-cirkel
De PDCA- (Plan-Doe-Controleer-Actie) cirkel is een reeks van activiteiten die worden uitgevoerd om te verbeteren. Dit begint met een onderzoek van de huidige situatie en de verzameling van gegevens teneinde een plan voor verbetering te formuleren. Als dit plan gereed is, wordt het uitgevoerd. Daarna wordt de uitvoering gecontroleerd om na te gaan of de verwachte verbetering heeft plaatsgevonden. Is dat het geval, dan wordt een vervolgactie ondernomen zoals normalisatie van de werkwijze om er zeker van te zijn dat de nieuwe ingevoerde methode voortdurend wordt toegepast, dit maakt de verbetering blijvend.
Handhaven volgens de SDCA-cirkel
Naast het verbeteren is een tweede taak van het management het handhaven. Hierbij is de SDCA- (Standaardisatie-Doe-Controleer-Actie) cirkel een essentieel hulpmiddel. Het is van belang dat de voordelen van de verbetering behouden blijven en de bestaande normen zijn gestabiliseerd voordat een volgende verbetering wordt ingezet. Na een doorgevoerde verbetering zal het proces aanvankelijk schommelingen vertonen. Het stabiliseren van de condities van het proces en het aldus vastleggen van de verbetering in nieuwe normen vindt plaats volgens de SDCA-cirkel.
Wisselwerking tussen PDCA- en SDCA-cirkel
Binnen het Kaizen-concept gaat het om de wisselwerkingtussen de respectievelijke cirkels. Door steeds opnieuw doorlopen van achtereenvolgende de PDCA- en de SDCA-cirkel zal continue verbetering plaatsvinden: zodra een verbetering als standaard is vastgelegd (volgens de SDCA-cirkel), wordt zij een uitdaging voor nieuwe plannen tot verdere verbetering (volgens de PDCA-cirkel).
Bron: Management van verbetering - kwaliteit in een veranderingsperspectief, J.W.M van Leeuwen & A.C. Waszink
Laatst aangepast op donderdag, 26 oktober 2017 05:59
Het visgraatdiagram volgens Jeroen Drontmann & Rob Bertels
Gepubliceerd in
Lean Six Sigma
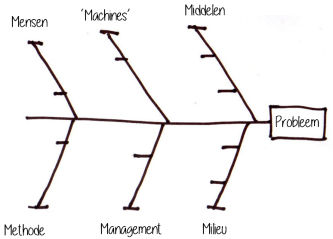
In het boek Persoonlijk succes schrijven Jeroen Drontmann en Rob Bertels hoe je met behulp van een Ishikawa- of visgraatdiagram als team samen aan de slag kunt gaan met het analyseren van de oorzaken van een probleem:

Analyseren van oorzaken
Ik wil:
Samen met het team mogelijke ooraken van een probleem analyseren. Hierbij ga ik gebruik maken van het Ishikawa- of visgraatdiagram.
Dus ik ga:
- Samen met het team proberen het probleem nauwkeurig definiëren. De formulering moet duidelijk zijn en door iedereen worden aanvaard. De uiteindelijke formulering schrijf ik (in maximaal één zin) op een flip-over-vel en dit hang ik voor iedereen zichtbaar op.
- Alle mogelijke oorzaken analyseren door gezamenlijk te brainstormen.
- Met behulp van inventariserende rondjes alle mogelijke oorzaken op een flip-over zetten. Ook hier is een duidelijke formulering belangrijk om 'krommunicatie' te voorkomen.
- Alle genoemde oorzaken ordenen in het Ishikawa- of visgraatmodel).
De structuur van dit moel dwingt ons door de indeling in vier grondoorzaken van een probleem niet tot overhaaste conclusies te komen. Het stelt dat een probleem meestal wordt veroorzaakt door ieder van de vier M's:
- de Mens (oorzaken bij personeel, gebruikers, mentaliteit/cultuur)
- de Machine (oorzaken bij machines en/of andere hulpmiddelen
- de Methode (oorzaken bij productiemethoden, de wijze van werken)
- het Materiaal (oorzaken bij materialen, de verwerkte grond- en hulpstoffen)
Binnen de rubrieken kan ik onderscheid maken tussen hoofdoorzaken en sub(verwante)-oorzaken.
De vier M's zijn hoofdgroepen en ik kan ze vrij vervangen door in ons organisatiejargon passende termen. Bij beleids-, plannings-, communicatie- en algemene managementproblemen kan ik de vier M's vervangen door een andere hoofdgroepenindeling (de vier O's): (externe) Omgeving, (interne) Opdrachtgevers, Operaties (projecten en methoden) en Ondersteuning (secretariaat, automatisering, enz.).
- Nadat de gebrainstormde oorzaken in één van de vier M's zijn ondergebracht, kijk ik samen met de groep welke M 'leeg' blijft en ga opnieuw brainstormen over oorzaken die we nog voor de 'lege' M kunnen bedenken.
- Het diagram aanvullen en definitief invullen. Tot slot bespreek ik het resultaat gezamenlijk en stel de definitieve analyse vast.
Bron: Persoonlijk succes, Jeroen Drontmann & Rob Bertels
Laatst aangepast op woensdag, 25 oktober 2017 08:06
Verbeteren volgens Bert Teeuwen
Gepubliceerd in
Lean Six Sigma
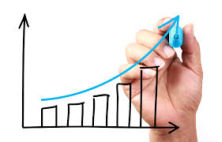
Bert Teeuwen beschrijft in zijn boek Dagstarts en Hoshin Kanri - Continu Leren en Verbeteren in de juiste richting met Dagstarts en Hoshin Kanri twee vormen van verbeteren: 'itererend verbeteren' en 'doorbraak verbeteren':
Volgens Teeuwen liggen er "Op weg naar de doeltoestand ... obstakels en belemmeringen van allerlei aard" en zijn er twee manieren om deze 'weg te nemen': (1) Itererend verbeteren door, één voor één wegnemen van obstakels en met kleine stapjes te leren en verbeteren, óf (2) doorbraak verbeteren: waarbij wordt ingestoken op een snelle doorbraak in de resultaten. In beide gevallen wordt de PDCA-cyclus gebruikt:

(1) Itererend verbeteren
[Itererend verbeteren is het een voor een wegnemen van alle die obstakels en belemmeringen die liggen op de weg naar de doeltoestand]. Voor elk obstakel zijn er verbeterideeën te bedenken. In een experiment (een test) zal blijken wat de effecten zijn en of een idee goed uitpakt.
De te volgen verbeterroutine (verbeterkata) is:
Plan
(a) Neem een obstakel en bestudeer die goed.
(b) Bedenk een experiment om dat obstakel nog beter te begrijpen, om die te verklaren of om die weg te nemen.
Do
(c) Voer het experiment uit.
Check
(d) Bestudeer de effecten van het experiment
Act
Borg de resultaten als die goed zijn
Plan
(a) Neem hetzelfde obstakel als die nog niet helemaal weg is, of een nieuwe.
(b) Bedenk nu weer een experiment om het obstakel beter te begrijpen, te verklaren of weg te nemen. Enzovoort.
Je ziet hier de PDCA-cyclus. Het gaat dus om een opeenvolgende reeks van PDCA-cycli. Welk experiment gaat komen, zal pas bekend zijn als de effecten van de laatste bestudeerd zijn.
Om deze cyclus niet het karakter te geven van zomaar wat voor de vuist weg experimenteren, is het raadzaam om bij elk obstakel op zoek te gaan naar de bronoorzaken met behulp van 5 x Waarom. Hoe meer kennis over de obstakels en hun bronoorzaken, hoe groter de kans op een succesvol experiment. Je moet kunnen uitleggen waarom voor het experiment gekozen is, welke effecten je ervan verwacht en waarom je die verwacht. Als die effecten positief zijn en de resultaten verbeteren, willen we toch graag weten waarom dat zo is.
Één obstakel tegelijk
Niet meer dan één obstakel tegelijk aanpakken, vindt Mike Rother, want anders zal je nooit weten welke van de oplossingen voor welk effect hebben gezorgd. Dan kun je niet leren van wat je doet. In theorie heeft hij gelijk. In de praktijk ligt het genuanceerder. Niet elke individuele oplossing creëert zijn eigen resultaat. Sommige oplossingen werken alleen in combinatie, of worden erdoor versterkt. De som van een paar oplossingen tegelijk uitvoeren levert soms meer op dan elk afzonderlijk.
(2) Doorbraak verbeteren
Verbeteren volgens de stap-voor-stap methodiek zoals hierboven beschreven is een uitstekende manier om continu te leren en te verbeteren. Er wordt niet alleen itererend verbeterd, maar vooral ook veel geleerd over het proces en de experimenten. Maar het is niet in elke situatie toepasbaar. Soms ontbreekt het aan tijd om zo bedachtzaam met klein stapjes te leren en verbeteren. Dan is een snelle doorbraak in de resultaten nodig en past de projectaanpak beter. Dat wil zeggen: projectmatig maar één PDCA-cyclus doorlopen. De omvang en aandacht die zo'n project krijgt roept veel meer een gevoel van urgentie op
Er zijn diverse manieren om projectmatig te verbeteren, zoals:
(i) A3-rapporten
(ii) Kaizenteams of verbeterteams
Ad (i) A3-rapporten
[Een A3-rapport is een op de PDCA-cirkel gebaseerd sjabloon op A3-formaat om een probleem tot de bodem uit te zoeken en op te lossen.] Een A3-rapport is compact, maar groot genoeg om de benodigde informatie op kwijt te kunnen.
De gebruiker van een A3-rapport doorloopt de volgende stappen:
Plan-fase
(1) Beschrijf het Wrobleem (wat is er aan de hand?)
(2) Beschrijf de situatie (Maak een schets of een foto van de situatie, voeg gegevens toe in de vorm van grafieken). Stel 5W2H-vragen, zoals Waar is het probleem? Hoe vaak? en Hoeveel?
(3) Zijn de basiscondities in orde?
(4) Stel een doel (Wat wil je bereiken? Maak het doel SMART.).
(5) Bepaal welke obstakels er zijn en vindt de bronoorzaken met 5 x Waarom.
(6) Bedenk oplossingen, en maak een actieplan om deze oplossingen in de praktijk uit te voeren.
Do-fase
Voer acties uit volgens plan
Check-fase
(7) Beoordeel de resultaten
Act-fase
(8) Borg de resultaten (Wat moeten we doen om te zorgen dat de oplossingen en het resultaat niet wegzakken?). En expandeer de resultaten (wat in het ene proces werkt, kan mogelijk ergens anders ook toegepast worden.
Ad (ii) Kaizenteams of Verbeterteams
Een kaizenteam is en kleinen multifunctionele groep mensen, die de opdracht krijgt om een afgebakend probleem uit het eigen werkveld te analyseren en op te lossen in een relatief korte periode. Lezen van zo'n kaizenteam hebben allemaal directe of indirecte invloed op het probleem. De route die het team volgt is de verbetercirkel, gebaseerd op PDCA, zoals de hierboven weergegeven 8-stappen cirkel. Een vergelijkbare variant is de DMAIC-cyclus.
Het verbeterteam is de opdrachtnemer. De opdrachtgever maakteen heldere opdrachtbrief met een probleemstelling, de opdrachtformulering, een doelstelling en een set randvoorwaarden waar de oplossingen aan moeten voldoen. Het team krijgt het mandaat om het probleem binnen de randvoorwaarden op te lossen.
De voortgang van hun werk is zichtbaar op een storyboard of zoals het eerder aangegeven A3-rapport.
(...)
Een kaizenteam kan in-een-keer een flinke klapper maken richting een doelstelling, door in een PDCA meerdere obstakels weg te nemen, met de verbeterkata gaat dat geleidelijker, obstakel voor obstakel. Aan de andere kant geeft een verbeterkata meer tijd om te leren en ligt de nadruk bij een kaizenteam meer op het oplossen van problemen en het halen van een verbeterdoelstelling. Daar wordt niet altijd gevraagd naar onderbouwing van het succes. Als het maar werk.
Bron: Dagstarts en Hoshin Kanri - Continu Leren en Verbeteren in de juiste richting met Dagstarts en Hoshin Kanri, Bert Teeuwen
Laatst aangepast op vrijdag, 13 april 2018 19:10
Toyota Kata volgens Bert Teeuwen
Gepubliceerd in
Lean Six Sigma
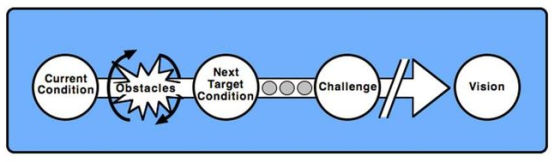
Bert Teeuwen beschrijft in zijn boek Dagstarts en Hoshin Kanri - Continu Leren en Verbeteren in de juiste richting met Dagstarts en Hoshin Kanri de Toyota Kata:

Toyota Kata
De verbeterroutine van Toyota zoals Mike Rother die beschrijft, kent vier fasen:
-
Begrijp de richting (formuleer in de vorm van een uitdaging: Wat zou het mooi zijn als ......).
-
Begrijp de huidige situatie.
-
Bepaal je eerste doeltoestand.
-
Verbeter continu, stap voor stap naar de doeltoestand
[In het bovenstaande schema zie je] de weg van de verbeterkata: vanuit de huidige situatie via doel-toestanden in de richting van de uitdaging. Tussen de doeltoestanden liggen de obstakels die weggenomen moeten worden. De obstakels tussen de 1e en de 2e doeltoestand zijn nog onbekend. De 2e doeltoestand bepaal je pas, als je de 1e is gerealiseerd. Ook is niet bekend hoeveel doeltoestanden er liggen op de weg naar de uitdaging.
En als je de 1e doeltoestand hebt gehaald, bepaal je de volgende doeltoestand. Niet eerder. Zo werk je experimenterend van doeltoestand naar doeltoestand in de juiste richting. Die juiste richting is een wenkend perspectief - een True North - dat een of meer jaren vooruit in de toekomst ligt, en dat past bij de missie en de visie van de organisatie. Die uitdaging hoeft niet haalbaar te zijn. De tussenliggende doeltoestanden wel. Volgens Rother ligt een doeltoestand steeds een paar weken tot een of meer maanden vooruit.
Het japanse woord kata betekent routine, maar dan het soort routine waar een topsporter naar streeft. Eindeloos herhalen van standaard bewegingen om die uiteindelijk onbewust en automatisch te kunnen doen. Onbewust bekwaam. Tot in de perfectie. Zo is ook de PDCA-cyclus een kata. Door die voortdurend tot te passen bij elke verbetering, ontstaat een vast patroon routine of automatisme.
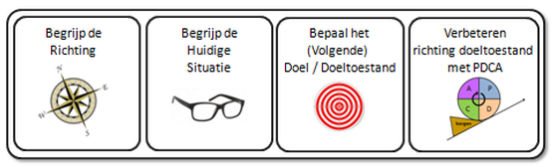
De vier fasen van de verbeterkata zie je nogmaals in de bovenstaande figuur.
Doeltoestand
Een doeltoestand is geen eindpunt, maar een opstapje naar een groter verder liggende doel - de uitdaging. Het woord doeltoestand (Target Condition) is meer dan alleen een meetbare doelstelling (Target). In een doeltoestand beschrijf je namelijk ook hoe het proces er dan uit ziet. Of, volgens Rother: "Hoe we het spel dan spelen." Een doeltoestand kan je visualiseren met een blokkendiagram of een Waardestroomanalyse, maar dan een van de zogenaamde future state, de toekomstige situatie. Daarin staan dan de proceskenmerken zoals flow, het gebruik van kanbans, de hoogte van de tussenvoorraden onderhanden werk, enzovoort. Om creatief en ruim te denken schets je na de huidige situatie niet direct de toekomstige situatie, maar eerst als tussenstap de ideale situatie (ideal state). De ideale situatie is de uitdaging of de True North. Zo schets je de doeltoestand (future state) vanuit het verder liggende en uitdagende perspectief.
Doeltoestanden komen niet in zijn geheel in de doelenmatrix. Dat zou niet kunnen omdat ze deels uit tekst bestaan. Alleen het meetbare deel, de doelstelling, wordt in de doelenmatrix opgenomen.
(...)
Niet iedereen is enthousiast over doeltoestanden. In zijn boek The Hoshin Kanri Forest vindt schrijver Javier Villalba-Diez dat het tegenstrijdig is om aan de ene kant te zeggen dat de weg naar de doeltoestand mistig en onduidelijk is en je nooit kunt weten welke obstakels je allemaal op de weg daarnaar te zult treffen, maar aan de andere kant wel een heldere en gedetailleerde doeltoestand kan formuleren. Dat kun je vanwege diezelfde mist dan toch ook niet? De obstakels verhinderen dan juist toch dat je zo'n doeltoestand kunt zien? Wie kan in de toekomst kijken? 'Tenzij je een kristallen bol bezit, heb je geen idee wat de details van de toekomstige situatie moeten zijn.' Het totale verbeterproces is 'emergent' (spontaan optredend of opkomend). Je kunt het niet plannen, alleen maar in goede banen leiden. Wat wel kan, is een meetbaar doel stellen op een prestatie-indicator.
Daartegenover kun je stellen dat doeltoestanden helemaal niet zo ver in de toekomst liggen. Een paar weken of maanden. Mogelijk dat je wel zóver vooruit kunt kijken.
In de praktijk zie ik dat doeltoestanden toch vooral doelstellingen zijn, aangevuld met randvoorwaarden waar het proces of de oplossingen aan moeten voldoen. Zoals met hoeveel mensen, de kosten, de voorraadniveaus, het kwaliteitsniveau, enzovoort. En dat blijkt goed te werken.
Bron: Dagstarts en Hoshin Kanri - Continu Leren en Verbeteren in de juiste richting met Dagstarts en Hoshin Kanri, Bert Teeuwen
Laatst aangepast op vrijdag, 25 januari 2019 16:57
Het Kano-model volgens Bert Teeuwen
Gepubliceerd in
Lean Six Sigma
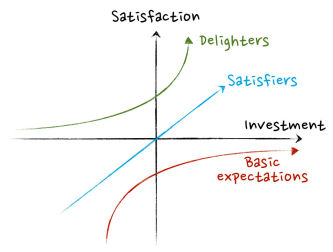
Bert Teeuwen beschrijft in zijn boek Dagstarts en Hoshin Kanri - Continu Leren en Verbeteren in de juiste richting met Dagstarts en Hoshin Kanri het Kano-model van Noriaki Kano:

Noriaki Kano deel in zijn model de productkenmerken die klanttevredenheid beïnvloeden op in drie groepen:
(1) Basisfactoren
Kenmerken waarmee je de klant niet verrast; het is zo basaal en vanzelfsprekend, dat de maximale vervulling van deze factoren nauwelijks opgemerkt wordt. Het ontbreken ervan geeft echter al snel een gevoel van ontevredenheid. Hoogst haalbare klanttevredenheidscijfer: een magere 6.
(2) Prestatiefactoren
Productkenmerken waarmee je je kunt onderscheiden van de concurrent. Het zijn voorspelbare factoren, waar een organisatie heel goed op kan scoren. Meestal noemt de klant als hem erom gevraagd wordt, deze kenmerken. Hoogst haalbare klanttevredenheidscijfer: 8.
(3) Enthousiasmefactoren
Kenmerken waarvoor geldt dat als producten of diensten deze factoren niet hebben, de klant dat niet merkt, want hij verwacht ze niet. Als ze er wel zijn, overtreft het de verwachtingen. Deze creëren de 'wauw'-ervaring. Het zijn echte innovaties. Het hoogst haalbare klanttevredenheidscijfer: een 10. Maar dat is tijdelijk. Klanten vinden deze productkenmerken al snel vanzelfsprekend en concurrenten kopiëren de innovatie. Het wordt een prestatiefactor of zelfs maar een basisfactor.
De eerste twee factoren zal de klant noemen. Enthousiasme-factoren vermoedelijk niet. De klant bedenkt het niet. Ze komen eerder uit marktonderzoek en de verbeelding en creativiteit van de medewerkers.
Bron: Dagstarts en Hoshin Kanri - Continu Leren en Verbeteren in de juiste richting met Dagstarts en Hoshin Kanri, Bert Teeuwen
Laatst aangepast op donderdag, 26 oktober 2017 06:02
De doelenmatrix volgens Bert Teeuwen
Gepubliceerd in
Lean Six Sigma
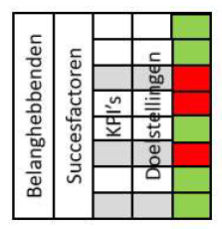
Bert Teeuwen beschrijft in zijn boek Dagstarts en Hoshin Kanri - Continu Leren en Verbeteren in de juiste richting met Dagstarts en Hoshin Kanri de doelenmatrix:

De doelenmatrix
Een doelenmatrix geeft het overzicht van de belangrijkste succesfactoren en prestatie-indicatoren voor elke belanghebbende. Helemaal links staan de belanghebbenden. Stel voor, of liever nog, aan elke belanghebbende de vraag: "Wanneer zijn we succesvol in jouw ogen?" of "Welke waarde creëren we voor je?" en "Wat zou je graag verbeterd willen zien?". Het antwoord daarop komt in de tweede kolom, de kritieke succesfactoren. Succesfactoren hoeven niet meetbaar te zijn. Het zijn vaak kreten als: "De dienstverlening moet sneller.", of "De producten moeten van hoge kwaliteit zijn.". In de derde kolom maak je de succesfactoren meetbaar met een prestatie-indicator. Alleen de belangrijkste succesfactoren en prestatie-indicatoren komen in de doelenmatrix. In de vierde kolom staan de resultaten van de afgelopen periode en in de volgende kolommen de doelstelling of de norm. Kritieke prestatie-indicatoren die moeten worden verbeterd, krijgen een doelstelling mee, de andere kritieke prestatie-indicatoren verlangen alleen actie als de norm wordt overschreden.
De doelenmatrix heeft de vorm van een Bowling-chart, met in de meest rechter kolom de actuele status van de kpi's, gevisualiseerd met verkeerslichtkleuren.
Er is een doelenmatrix voor de organisatie als geheel nodig. Dat is het dashboard voor de totale organisatie. Daarnaast maakt elke afdeling har eigen doelenmatrix, die daarmee in lijn ligt. De kpi's in de doelenmatrix zijn voornamelijk resultaat-indicatoren en effect-indicatoren.
Denk bij het samenstellen van een doelenmatrix aan het volgende:
-
Begrijp het proces en de producten en diensten.
-
Weet wat de belanghebbenden belangrijk vinden.
-
Ken de markt en wees innovatief.
Bron: Dagstarts en Hoshin Kanri - Continu Leren en Verbeteren in de juiste richting met Dagstarts en Hoshin Kanri, Bert Teeuwen
Laatst aangepast op donderdag, 26 oktober 2017 06:02
DMAIC volgens MKPC
Gepubliceerd in
Lean Six Sigma
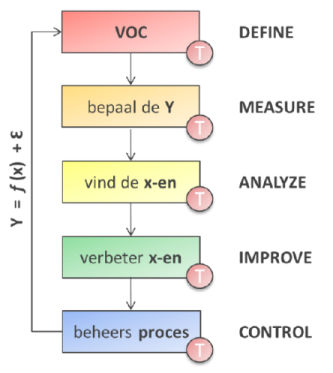
MKPC visualiseert en beschrijft de DMAIC-fasen op boven-/onderstaande wijze:

[1] Define (business vraagstuk)
=> VOC
01 Selecteer en start het project 02 Bepaal de klantwens en defects
[2] Measure (statistisch vraagstuk)
=> Bepaal de Y
03 Meten wat de klant wil 04 Toets de meetnauwkeurigheid
[3] Analyze (statistische oplossing)
=> Vind de X-en
06 Bedenk mogelijk oorzaken 07 Bepaal waarschijnlijke oorzaken 08 Valideer hoofdoorzaken
[4] Improve (business oplossing)
=> Verbeter de X-en
09 Bepaal de beste oplossing 10 Toets het meetsysteem
[5] Control (beheersen oplossing)
=> Beheers het proces
11 Meet nieuwe procesprestatie 12 Borgen oplossingen
T = Tollgate
Bron: Structuur Lean Six Sigma Blackbelt project
Bewaren
Laatst aangepast op dinsdag, 24 oktober 2017 07:05
|