Six Sigma volgens Marijn Mulders
Gepubliceerd in
Lean Six Sigma
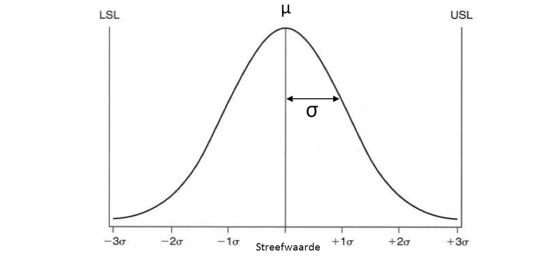
Marijn Mulders beschrijft in zijn boek Business & Managementmodellen de theorie van Six Sigma als volgt:

Achtergrond Six Sigma is een methode om de kwaliteit van de processen in een onderneming te verbeteren. Elke keer dat ven proces wordt uitgevoerd kan er een variatie optreden ten opzichte van de resultaten van de vorige keer.
Deze afwijkingen worden `defects' genoemd en uitgedrukt in het aantal afwijkingen per miljoen mogelijkheden ofwel 'Defects Per Million Opportunities (DPMO)'. De afwijking uitgedrukt in sigma komt uit de statistiek, waarbij de waarde van sigma oploopt van 0 tot en met 6. Het streven hierbij is om zo weinig mogelijk afwijkingen te hebben. Bij zes sigma zijn er maximaal 3,4 afwijkingen per miljoen kansen waarbij 99,9997% goede producten geproduceerd wordt. Een belangrijk aspect bij deze methode is dat er uitgegaan wordt van wat de wensen van de klant zijn en dat de afwijkingen gebaseerd zijn op keiharde metingen en niet op het gevoel of gemiddelde waarden. Bij deze methode wordt een vast stappenplan doorlopen om de procesverbeteringen te realiseren. Het betreft hier de bedrijfsprocessen van de onderneming, waarbij het niet uitmaakt of het een productiebedrijf of een dienstverlenend bedrijf betreft. Het stappenplan bestaat uit de stappen Define, Measure, Analyze, lmprove en Control, afgekort DMAIC.
Toepassing Het Six Sigma-model wordt uitgevoerd op basis van vijf stappen:
1 Define
Alvorens te kunnen gaan meten dient eerst het probleem goed in kaart gebracht te worden. Bovendien dient het werkgebied afgebakend te worden om het onderzoeksgebied te versmallen zodat zo snel mogelijk meetbare doelstellingen kunnen worden bereikt. Als tweede zullen de betrokken medewerkers geselecteerd moeten worden om het proces in detail te onderzoeken en verbeteringen voor te stellen.
2 Measure
De tweede stap is het verzamelen van gegevens en de voorbereidingen treffen voor het analyseren en interpreteren van de gegevens.
3 Analyze
Na documentatie en verificatie van de gegevens kan de analyse ervan beginnen. Activiteiten waarbij de medewerkers onvoldoende in staat zijn effectief te handelen of niet erin slagen een efficiënte controle toe te passen, worden geselecteerd en geïdentificeerd.
4 Improve
Per activiteit uit de analyse-stap wordt vastgesteld op welke wijze deze verbeterd kan worden.
5 Control
De laatste stap is het uitwerken van de verbeterdoelstellingen en deze implementeren op de werkvloer. Daarnaast wordt een systeem opgezet om handhaving van de verbeteringen te waarborgen.
Om deze stappen goed uit te kunnen voeren zijn medewerkers (intern en extern) nodig met kennis van de methode. Het project dient vanuit het (top) management ondersteund te worden. Binnen Six Sigma zijn er vier rollen te onderscheiden:
• Master Black Beits: opleiders, meestal van een extern bureau.
• Black Beits: projectleiders, met een gespecialiseerde opleiding (1% van personeel).
• Green Belts: projectmedewerkers met een basisopleiding (10% van personeel).
• Projectmedewerkers: medewerkers met alleen een interne opleiding.
Resultaat De resultaten die de toepassing van deze methode kan opleveren zijn groot. Elk proces van de onderneming kan met dit model verbeterd worden. Inzet van dit model op de kritische processen helpt een onderneming om haar doelstellingen beter te realiseren. Voorbeelden van verbeteringen zijn:
- extreem laag foutenniveau;
- minstens 99% klanttevredenheid
- hogere productiviteit
- drastische doorlooptijdvermindering
- spectaculaire kostenreductie
- totale aanpak met betrekking tot kwaliteit
Aandachtsgebieden Hoewel Six Sigma bijna altijd leidt tot een goed resultaat, dient een afweging gemaakt te worden met betrekking tot de investering in tijd en geld. De methode vergt tijd en energie van de medewerkers van de onderneming op hoog en laag niveau. Literatuur
Bron: Business & Managementmodellen, Marijn Mulders
Laatst aangepast op maandag, 14 februari 2022 20:00
LSS: geschiedenis Six Sigma
Gepubliceerd in
Lean Six Sigma
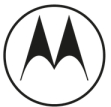

Het was 1979 toen Art Sundrey bij Motorola zijn vermaarde woorden sprak: 'Our quality stinks'. Dat was het begin van een immense verbeterinspanning bij het bedrijf. In een aantal jaren werd een verbeterprogramma opgebouwd, dat momenteel de wereldstandaard is voor betere prestaties.
In de jaren tachtig stond Bob Galvin, CEO bij Motorola, voor de uitdaging om bij Motorola een tienvoudige verbetering te realiseren in vijf jaar. Bill Smith bedacht de naam voor de verbeteringsmaatregelen: Six Sigma. Door de inspanning van Bill Smith werden de eerste programma's meer datageoriënteerd en door de komst van Mikel J. Harry ontstond een standaardstructuur van werken die we nu kennen als de DMAIC-cyclus. Uit zijn koker kwamen ook de namen van de spelers van het Six Sigma-programma als Black Belt, Green Belt, Master Black Belt en Champion.
Harry, bestudeerde de variaties in verscheidene processen bij Motorola. Al snel kwam hij tot de conclusie dat een te grote variatie een lagere klanttevredenheid met zich meebracht. Bovendien bleken de producten die onmiddellijk correct geproduceerd waren en geen herwerking vereisten, later minder problemen op te leveren bij de klant. Harry en zijn collega’s bekeken de processen die het meest te kampen hadden met variatie en ontwikkelden een heel gamma tools om deze variatie te reduceren en te controleren. Op die manier werd de effectiviteit en de efficiëntie van de processen gevoelig verbeterd.
Het totale programma ontwikkelde zich vooral na de adoptie van Six Sigma dor Jack Welch. Jack Welch Six Sigma organisatiebreed te implementeren. Jack Welch besloot dat zijn bedrijf in een tijdspanne van vijf jaar moest opereren op Six Sigma-niveau. Deze beslissing bracht investeringen van honderd miljoen dollar met zich mee voor de opleiding van het personeel, maar de aanpak zorgde voor spectaculaire kostenbesparingen voor de onderneming. In minder dan 2 jaar na de allereerste applicatie van Six Sigma, had GE reeds $320 miljoen aan kostenbesparingen gerealiseerd. In 1998 was dit bedrag al opgelopen tot $750 miljoen.
Bij Six Sigma staat de klanttevredenheid centraal. Om te bepalen waar mogelijke verbeteringen mogelijk zijn, is het essentieel goed te luisteren naar de klant. Wanneer de voormalige CEO van GE Jack Welch klaagde dat “his frontline managers had their face towards the CEO and their ass towards the customers” benadrukte hij wat essentieel is in Six Sigma: het is de klant die bepaalt wat kwaliteit inhoudt.
Om de 'Voice of the Customer' (VOC) te kunnen verzamelen moeten in de eerst plaats de klanten van de onderneming geïdentificeerd worden om te weten aan wiens noden de onderneming moet voldoen. Indien er meerdere segmenten te ontdekken zijn, moet naar hun verschillende VOC geluisterd worden en worden de verschillen in hun wensen onderzocht.
Zie ook: De geschiedenis van Lean Six Sigma
Bron:
Laatst aangepast op maandag, 14 februari 2022 19:57
5S volgens Masaaki Imai
Gepubliceerd in
Lean Six Sigma

Masaaki Imai beschrijft in zijn boek Kaizen - de sleutel van de Japanse concurrentie het Lean-instrument van '5S' als volgt:

Stap-1 Seiri (stel orde op zaken)
- Onderhanden werk
- Onnodige gereedschappen
- Ongebruikte machines
- Foutieve producten
- Papieren en documenten
Maak verschil tussen nodige en onnodige zaken en schaf onnodige af.
Stap-2 Seiton (berg zaken ordelijk op)
Zaken moeten ordelijk worden opgeborgen zodat ze, indien nodig, gereed zijn voor gebruik.
Stap-3 Seiso (maak schoon)
Houd de werkplek schoon
Stap-4 Seiketsu (persoonlijke netheid)
Maak er een gewoonte van schoon en netjes voor de dag te komen, te beginnen met jezelf.
Stap-5 Shitsuke (discipline)
Houdt de procedures aan die voor de werkplek gelden.
Bron: Kaizen, Masaaki Imai
Laatst aangepast op dinsdag, 04 januari 2022 11:30
Management volgens Russell Ackoff
Gepubliceerd in
Lean Six Sigma
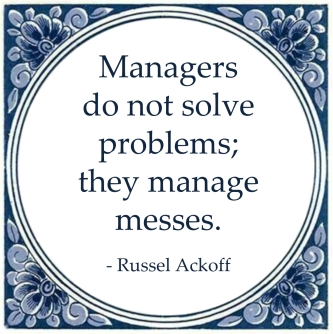

Managers are not confronted with problems that are independent of each other, but with dynamic situations that consist of complex systems of changing problems that interact with each other. I call such situations *messes*.
(...)
Problems are abstractions extracted from messes by analysis; they are to messes as atoms are to tables and chairs. We experience messes, tables, and chairs; not problems and atoms.
(...)
Because messes are systems of problems, the sum of the optimal solutions to each component problem taken separately is *not* an optimal solution to the mess. The behaviour of a mess depends more on how the solutions to its parts interact......than on how they act independently of each other. But the unit in OR [Operational Research] is a problem, not a mess. Managers do not solve problems; they manage messes.
Russel Ackoff
Laatst aangepast op donderdag, 16 december 2021 19:15
Doorlooptijd(verkorting) volgens Anne Tijdhof
Gepubliceerd in
Lean Six Sigma
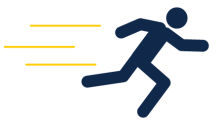
Anne Tijdhof deed onderzoek naar het verbeteren van doorlooptijden in een ziekenhuis. Hieronder een aantal fragmenten die wellicht ook buiten de muren van een ziekenhuis bruikbaar zijn:

Capaciteiten zijn productiemiddelen die bij de totstandkoming van productie gebruikt worden, maar niet verbruikt of verwerkt worden. Voorbeelden van capaciteiten zijn personeel, ruimte en apparatuur. Een belangrijke capaciteitssoort is de bottleneck capaciteitssoort. Dit is de capaciteit die het eerste op is en waardoor de productie niet verder opgevoerd kan worden.
Doorgaans probeert men deze capaciteitssoort maximaal te benutten. Een capaciteitssoort kan ook gedeeld zijn. Dit is het geval als verschillende productlijnen gebruik maken van de desbetreffende capaciteitssoort. Een voorbeeld van een ‘shared resource’ is bijvoorbeeld de OK. (...) Door de verschillende ‘shared resources’ ontstaan er kris-kras stromen. Capaciteiten kunnen continu en discontinu beschikbaar zijn. Een ziekenhuisbed is een voorbeeld van een continu beschikbare capaciteitssoort. Een onderzoeksafdeling daarentegen, die op een bepaalde tijd open is, is een voorbeeld van een discontinue capaciteitssoort.
Een laatste onderscheid ... is de initiërende versus de volgende capaciteitsoort. Een capaciteitssoort wordt initiërend genoemd als productie op deze capaciteitssoort tot gevolg heeft dat er ook productie wordt gegenereerd wordt op andere capaciteitssoorten, de volgende capaciteitssoorten.
Het proces dat een patiënt met pijn op de borst op de polikliniek doorloopt kan grafisch worden weergegeven door middel van process mapping. Dit is een techniek die leidt tot identificatie van bottlenecks en probleemgebieden in een proces en daarmee tot reductie van doorlooptijd, benodigde ruimte, benodigde resources, aantal processtappen, proceskosten en managementkosten. Daarnaast dient het als een goede basis voor het ontwerpen van een totaal nieuw proces.
Laeven et al., (2000) noemt drie manieren om de doorlooptijd te beïnvloeden. Ten eerste een toename van de verwerkingscapaciteit. Dit kan door extra gelden beschikbaar te stellen, een verbeterde planning en door een toename van de capaciteit (bijvoorbeeld meer FTE’s). Een tweede manier is het beperken van de instroom, bijvoorbeeld door het vragen van een eigen bijdrage of door een goede voorlichting en communicatie naar verwijzers en patiënten. Andere manieren om invloed uit te oefenen op de vraag is ontkoppeling van binnenkomende patiënten. Ook door het maken van urgentiecategorieën kan er met de vraag gespeeld worden (De Vries en Hiddema, 2001). Een laatste manier om de doorlooptijd te beïnvloeden is volgens Laeven et al., (2000) de herverdeling van vraag en aanbod. Dit betekent dat patiënten naar een ander ziekenhuis gaan waar de wachttijd korter is. Maar problemen van een lange doorlooptijd kan ook gezocht worden in de organisatie van het zorgproces. Een capaciteit die bijvoorbeeld wacht is inefficiënt, deze wordt dan namelijk niet gebruikt (Van Merode, 2002). Een manier om vraag en aanbod beter op elkaar af te stemmen is het gebruik van buffers. Er kan zowel aan de vraag- als aan de aanbodzijde gebruik worden gemaakt van buffers. Aan de vraagzijde is dit de factor tijd, de patiënt die wacht tot hij/zij aan de beurt is. Aan de aanbodzijde wordt de beschikbaarheid van capaciteit als buffer gehanteerd. Dit leidt tot een hogere servicekwaliteit, maar zet de doelmatigheid onder druk. Bij buffervorming aan de vraagzijde gebeurt precies het tegenovergestelde (De Vries en Hiddema, 2001). Een andere manier om een doelmatige benutting van capaciteit te realiseren is batching. Door uit te gaan van een serie van patiënten die binnen een batch geholpen wordt kan men wisseltijden vermijden (Vissers, De Vries, Bertrand, 2001). Voor een visuele weergave van de factoren die een rol spelen bij doorlooptijdproblemen, zie onderstaande figuur De factoren in de grijze vakken komen in dit onderzoek nader aan bod.
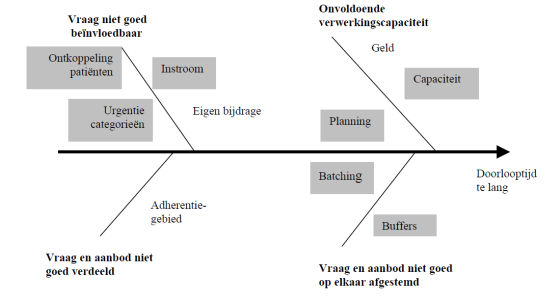
Uit bovenstaande figuur blijkt dat er uit de literatuur vier clusters van factoren zijn die van invloed kunnen zijn op een lange doorlooptijd. Ten eerste geen goede verdeling van vraag en aanbod. Dit kan bijvoorbeeld betekenen voor de polikliniek Cardiologie dat er teveel huisartsen verwijzen naar het Erasmus MC. Tijdens dit onderzoek wordt hier verder niet op ingegaan. Een tweede manier om invloed uit te oefenen op de doorlooptijd is het beïnvloeden van de vraag door bijvoorbeeld het vragen van een eigen bijdrage. In dit onderzoek wordt het vragen van een eigen bijdrage niet meegenomen als optie om de doorlooptijd te verkorten. Wel wordt er daar waar noodzakelijk aandacht besteedt aan de instroom, urgentiecategorieën en ontkoppeling van patiënten. De instroom van patiënten heeft betrekking op het aantal patiënten dat de polikliniek Cardiologie bezoekt. Bij het maken van urgentiecategorieën wordt gekeken naar een eventuele opsplitsing in spoed patiënten en electieve patiënten, waardoor er een ontkoppeling van patiënten plaats vindt. Een derde cluster van factoren om de doorlooptijd te beïnvloeden heeft betrekking op de verwerkingscapaciteit. Het verhogen van de verwerkingscapaciteit kan men bijvoorbeeld doen door meer geld beschikbaar te stellen. Ook dit zal in dit onderzoek geen optie zijn om invloed uit te oefenen op de doorlooptijd. Wel wordt er aandacht geschonken aan de capaciteit en de planning als variabelen om invloed uit te oefenen op de doorlooptijd. Een laatste belangrijk cluster van factoren die van invloed is op de doorlooptijd is het afstemmen van vraag en aanbod. Dit kan door de toepassing van batching en buffers. Deze twee variabelen worden in dit onderzoek meegenomen als beïnvloedbare factoren.
(...)
Voorstellen voor verbetering met behulp van de literatuur
Een eerste manier om de doorlooptijd te verkorten is het verhogen van de verwerkingscapaciteit. [De] verwerkingscapaciteit is afhankelijk van de beschikbare capaciteit en van het budget. Maar ook een goede planning kan de verwerkingscapaciteit doen laten toenemen. Het budget wordt in dit onderzoek gezien als een vaste variabele die niet beïnvloedbaar is, evenals de beschikbare capaciteit die is weergeven in tabel 3. De verwerkingscapaciteit kan worden verbeterd door een betere planning. Dit komt aan bod bij de ontwikkeling van de verschillende verbeter scenario’s. Een tweede manier om de doorlooptijd te verkorten is het beïnvloeden van de vraag. Dit kan gedaan worden door een goede voorlichting te geven aan verwijzers en patiënten. Dit betekent dat bij het herinrichten van het zorgproces voor patiënten met pijn op de borst een goede communicatie naar de verwijzers van belang is, zodat de juiste groep patiënten de juiste onderzoeken ondergaan. Herverdeling van vraag en aanbod is een andere manier uit de literatuur om de doorlooptijd te verkorten. Dit betekent dat de patiënten naar een ander ziekenhuis gaan. Er van uitgaande dat de polikliniek geen cliënten wil verliezen is dit dus geen optie. Wat zich mogelijk wel zou kunnen voordoen als het zorgproces goed georganiseerd is en de doorlooptijd verkort is dat dit patiënten aantrekt. Een laatste manier uit de literatuur om de doorlooptijd te beïnvloeden is het beter op elkaar afstemmen van vraag en aanbod. Ook hier wordt aandacht aan besteed bij de verschillende scenario’s.
Bron: Een 'Fast Track' polikliniek - onderzoek naar de doorlooptijd van patiënten met pijn op de borst in het Erasmus MC, Anne Tijdhof
Laatst aangepast op donderdag, 02 december 2021 19:56
Pull vs. push volgens Jay Arthur
Gepubliceerd in
Lean Six Sigma
Laatst aangepast op donderdag, 02 december 2021 19:56
Takttijd volgens Marcel van Assen
Gepubliceerd in
Lean Six Sigma
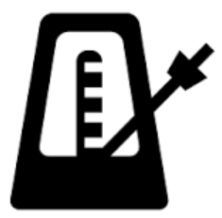
Marcel van Assen beschrijft in zijn boek Handboek Lean management het Lean-concept takttijd:

Takttijd [is] het ritme (tempo) van het proces waarin producten gemaakt moeten worden om precies aan de klantvraag te voldoen. De takttijd is een target-cyclustijd waarbinnen het werk bij elke schakel (operator, machine, station) in het proces moet worden uitgevoerd zodat - binnen een bepaalde productieperiode - precies wordt voldaan aan de klantvraag. De takttijd is derhalve gelijk aan de beschikbare productietijd gedeeld door het aantal te produceren eenheden (volgens de klantenwens):
takttijd = beschikbare productietijd / aantal te produceren eenheden
Het doel van een takttijd is het ontwerp van een proces, zodanig dat de productie-output is afgestemd op de klantvraag. Met de takttijd kan bepaald worden welke minimale hoeveelheid bedrijfsmiddelen (mankracht, gereedschap, machines) daarvoor nodig is. De takttijd is dan een ontwerptarget voor een efficiënt, evenwichtig proces. In operationele zin fungeert de takttijd als leidraad om de operatie op te sturen, als een metronoom om de taken, activiteiten en bewegingen in het proces te coördineren. Het werken in een vast ritme ondersteunt ook het visuele management.
Het denken in takttijden past vooral bij een productgeoriënteerde layout met unidirectionele flow (stroming), omdat het uitgaat van een vast procestempo in een bepaalde periode zodat de output precies gelijk aan de klantvraag is. Bij complexere processen en routeringen waarbij producten één of meerdere keren terugkeren in het proces, en bij een sterk wisselende klantvraag, is het bepalen van een takttijd minder eenvoudig of praktisch ondoenlijk.
Bron: Handboek Lean management - aanpak, concepten en modellen voor het succesvol toepassen van Lean, Marcel van Assen
Laatst aangepast op donderdag, 02 december 2021 19:55
De geschiedenins van Lean: de T-Ford
Gepubliceerd in
Lean Six Sigma
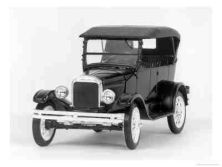
De ontwikkeling en opkomst van de T-Ford heeft een belangrijke rol gespeeld bij de invoering van het Toyota Production System (TPS) en Lean. In het boek Organisatiestructuur en arbeidsplaats beschrijft Jan in 't Veld beknopt de geschiedenis van de T-Ford:

De eerste industriële toepassing van lijnproductie op grote schaal is gerealiseerd door Henri Ford. In 1908 brengt hij zijn T-model uit. In 1909 annoceert hij dat zijn bedrijf voortaan nog slechts één model, namelijk de T-Ford, zal produceren en dat het chassis voor alle wagens exact hetzelfde zal zijn. Hij maakt hierbij de beroemde opmerking: 'Any customer can have a car painted any colour he wants so long as it is black'.
Begin 1913 doet hij het eerste experiment op kleine schaal met een productielijn voor de vliegwielmagneet. Hijzelf zegt dat het idee voor een bewegende lijn min of meer afkomstig is uit de slachthuizen van Chicago. Daar hangen de varkens en koeien aan een bewegende ketting. Het zijn een soort démontagelijnen die men daar al sinds 1870 gebruikt. Voordat Ford zijn experiment begint, wordt die vliegwielmagneet door één man in elkaar gezet in ca. 20 minuten. In de lijn gebeurt dat in 7 minuten en later zelfs in maar 5 minuten. In 1914 wordt het lijnprincipe ook toegepast op de chassisbouw. De beste tijd voor een complete samenbouw van een chassis was tot dan toe 12 uur 28 min. In een lijnstructuur wordt dit uiteindelijk teruggebracht tot 1 uur 33 min.
Het productietempo wordt hoger en de lijn langer en eind 1914 maakt Ford al 1000 auto's per dag, d.w.z. 300.000 per jaar. In 1919 is dat gestegen tot 2.000.000 wagens per jaar. De prijs wordt verlaagd van $ 780 in 1910 tot $ 290 in 1924. Deze massaproductie is mogelijk geworden door een ver doorgevoerde scheiding tussen voorbereiding en uitvoering. De coördinatie tussen de diverse handelingen en de vereiste uitwisselbaarheid van de onderdelen zijn volledig vastgelegd in de gereedschapmakers. Men heeft een achturige werkwag, een relatie hoog loon en een vorm van winstdeling. Wanneer de productie van de T-Ford in 1927 wordt gestopt, zijn er in totaal 15 miljoen van geproduceerd en heeft Ford het grote publiek ervan overtuigd dat massaproductie niet samen hoeft te gaan met inferieure kwaliteit.
Bron: Organisatiestructuur en arbeidsplaats, J. in 't Veld
Laatst aangepast op donderdag, 02 december 2021 19:55
Lean volgens Jan Heunks
Gepubliceerd in
Lean Six Sigma

In zijn boek Lean IT probeert Jan Heunks Lean te vertalen naar de vraag/aanbod-organisatie binnen de IT. Binnen zijn aanpak onderkent Heunks zeven kritieke succesfactoren die 'beslissend zijn voor het al dan niet halen van het uiteindelijke doel: het maximaliseren van waarde voor de klant door het minimaliseren van verspilling':
-
Klantfocus (vraagketen).
-
Waardecreatie (waardeketen).
-
Leveringsfactoren (leveringsketen).
-
Waardecontext (middelen en vermogen).
-
Behendigheid (agility).
-
Leiderschap (zichtbare aanwezigheid).
-
Gedrag & attitude (mindset).
Heunks baseert zijn model op het vijfstapsdenkproces dat de basis vormt voor Lean:
-
Waarde.
-
Waardestroom.
-
Doorstroming.
-
Vraagsturing.
-
Perfectie.
Bron: Lean IT, Jan Heunks
Laatst aangepast op donderdag, 02 december 2021 19:55
Waardetoevoeging vs. verspilling binnen Lean
Gepubliceerd in
Lean Six Sigma
Laatst aangepast op donderdag, 02 december 2021 19:55
|