Lean leiderschap volgens Jan Wijnand Hoek (2)
Gepubliceerd in
Lean Six Sigma
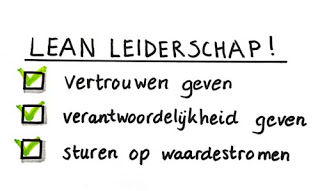
Jan Wijnand Hoek stelt in het artikel Management overtuigingen die Lean Leiderschap in de weg staan voor om drie beperkende managementovertuigingen te vervangen door Lean Leiderschap:

De traditionele aanpak
De volgende 3 managementovertuigingen staan Lean Leiderschap bij het bouwen van een Lean cultuur het meest in de weg:
-
Controleren.
-
Doorbelasten.
-
Sturen op budget.
In de basis zijn controleren, doorbelasten en sturen op budget alle vormen van “voorkomen van kosten” door de verantwoordelijkheid en deskundigheid van medewerkers te vervangen voor geformaliseerde managementbeslissingen in de vorm van regels en maatregelen.
Medewerkers geven om hun werk. Ze willen het goed doen en graag de klant het best mogelijke geven. De [bovengenoemde] managementinstrumenten staan daarbij stevig in de weg.
(...)
Controles, doorbelasting en sturen op budget zijn als managementinstrumenten geformaliseerd en diep ingeworteld in bijna elke organisatie. Ze zijn verworden tot het managementsysteem. Zo werken wij hier. De grootste uitdaging van elke Lean Leider is uiteindelijk dit inmiddels hardnekkige traditionele systeem te veranderen naar een Lean systeem ...
Het eerste wat Lean Leiders te doen staat is vertrouwen en verantwoordelijkheid geven aan de werkvloer door o.a. het:
-
Opruimen van een groot deel van de regels en controles.
-
Stoppen van de nutteloze doorbelastingssystematiek.
-
Sturen op budget om te buigen naar sturen op de waardestromen
Hiermee wordt de weg voor medewerkers vrij gemaakt om processen te kunnen verbeteren en zodoende weer succesvol te kunnen zijn in hun werk.
(...)
Het sturen op budgetten moet worden vervangen door sturen op waardestromen, door als Lean Leider de rol van waardestroom eigenaar op je te nemen. Een waardestroom eigenaar ondersteund de werkvloer met het bouwen van processen, waarin vakmensen in staat worden gesteld de juiste kwaliteit te leveren aan de vervolgstap van het proces. Foutvrij van mij noemt Scania dat. Toyota noemt dit QIP (Quality Into Proces). Dit houdt in dat vakmensen in staat worden gesteld zelf te beoordelen of ze de juiste kwaliteit doorgegeven aan de volgende processtap. Via QIP neemt de kwaliteit van proces zodanig toe dat de kosten vanzelf dalen.
Bron: Management overtuigingen die Lean Leiderschap in de weg staan, Jan Wijnand Hoek
Laatst aangepast op zaterdag, 02 december 2017 08:32
Lean leiderschap volgens Jan Wijnand Hoek
Gepubliceerd in
Lean Six Sigma
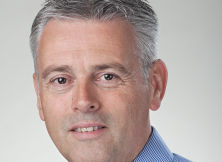
In het artikel De kern van Lean Leiderschap in een aantal praktische punten, Jan Wijnand Hoek stelt Jan Wijnand Hoek dat Lean leiderschap bestaat uit vier aspecten:

In de kern wordt het volgende van een Lean Leider verwacht:
-
Sturen op het WAT en WAAROM (ware noorden, visie, richting geven), dat betekent geen brandjes blussen of oplossingen aandragen. Op de werkvloer vind je de juiste expertise en het vakmanschap om invulling te geven aan de HOE-vraag.
-
Sturen op waardestromen en kwaliteit i.p.v. sturen op budget, support de Kaizens en geef tijd voor het verbeteren van processen als onderdeel van het reguliere werk (verbeteren is werktijd).
-
Vertrouwen geven en verantwoordelijkheid geven in plaats van controleren, stimuleer experimenteren en leren (van gemaakte fouten). Een lean organisatie is een lerende organisatie. Werkplezier is het werk goed kunnen doen en is een belangrijke voorwaarde voor tevreden klanten.
-
Werkvloeren en successen vieren!
Bron: De kern van Lean Leiderschap in een aantal praktische punten, Jan Wijnand Hoek
Laatst aangepast op zaterdag, 02 december 2017 08:32
Policy deployment volgens DeMeulmeester & Callewier
Gepubliceerd in
Lean Six Sigma
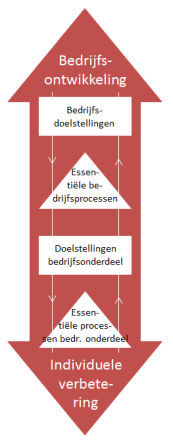
Erik DeMeulemeester en Dominiek Callewier beschrijven in het boek Integrale kwaliteitszorg - concepten, methoden en technieken het Lean-instrument Policy deployment (Hoshin planning):

Policy deployment
Het topmanagement heeft behoefte aan een methode om te zorgen dat hun plannen en strategieën succesvol worden uitgevoerd binnen de organisatie. Policy deployment (hoshin planning) is her een middel toe.
Het is een plannings- en uitvoeringssysteem dat de belangrijkste elementen aanreikt om het bedrijf vooruit te helpen in het streven naar het bereiken van de langetermijndoelstellingen. Vertrekkend vanuit de doelstellingen van de organisatie worden gepaste strategieën en maatregelen geformuleerd, waarna de organisatie zich richt op het bereiken van deze doelstellingen en gestelde prioriteiten. Policy deployment is een hiërarchisch systeem dat vanuit het topmanagement naar beneden toe werkt (top-down.
(...)
Policy deployment en procesmanagement zijn complementaire aanpakken om cruciale processen te identificeren en om het eens te worden over uitdagende doelstellingen om deze processen te verbeteren. Continue verbetering is de systematische inspanning waardoor processen op een hoger niveau van performantie worden gebracht.
(...)
Verbeteringsprocessen moeten worden gepland: stel de doelen vast, ontwerp plannen om deze doelen te bereiken, zorg voor de middelen, ken verantwoordelijkheden toe en volg de vooruitgang.
(...)
De klantenwensen en prioriteiten van het bedrijf moeten worden vertaald in doelen voor teams en individuen. Op elk niveau in de organisatie en bij elke schakel in de keten moeten processen worden geanalyseerd en dient overeenstemming te bestaan over de doelstellingen. De normale organisatiestructuur met barrières tussen niveaus en functies is doorgaans niet toereikend om dit te bereiken. Veel kwaliteitsverbeteringsacties liggen buiten het terrein van de gevestigde werkgroepen. Daarom [is het nodig] een extra netwerk te realiseren om informatie door te geven en overeenstemming te bereiken ten aanzien van prioriteiten over verschillende functies en niveaus heen. Daarom wordt de organisatie versterkt met bruggen:
- bruggen tussen niveaus: policy deployment
- bruggen tussen functies: procesmanagement
Bij policy deployment worden bedrijfsdoelstellingen door de opeenvolgende lagen in de organisatie heen vertaald en gecommuniceerd. Bij procesmanagement worden de wensen van de klanten naar de opeenvolgende schakels in het bedrijfsproces vertaald en gecommuniceerd. De combinatie van beide bruggen creëert duidelijkheid en samenhang die nodig zijn om inspanningen te richten op de bedrijfsprioriteiten en op het vervullen van de klantenwensen. Continue verbetering versnelt de ontwikkeling van de organisatie door continu nieuwe verbeteringsopportuniteiten te zoeken.
Policy deployment
Policy deployment verschaft een structuur voor delegatie en participatie. Het is een neerwaarts én opwaarts proces dat doelstellingen op alle niveaus op één lijn brengt.
In overleg tussen de verschillende niveaus worden de prioriteiten gesteld, wordt de uitvoerbaarheid van plannen getoetst en wordt betrokkenheid van individuen en teams bewerkstelligd. Het proces moet in twee richtingen werken. Het management geeft aan in welke gebieden met prioriteit verbeteringen moeten worden bereikt en zet daarvoor tijd en middelen in. Medewerkers worden aangemoedigd initiatieven te nemen die in overeenstemming zijn met deze prioriteiten. Policy deployment zorgt ervoor dat iedereen in het bedrijf in dezelfde richting werkt, op weg naar duidelijk beschreven en uitgezette doelen.
Bron: Integrale kwaliteitszorg - concepten, methoden en technieken, Erik DeMeulemeester & Dominiek Callewier
Laatst aangepast op zaterdag, 02 december 2017 22:07
SOP volgens Webers, Van Engelen & Luijben
Gepubliceerd in
Lean Six Sigma
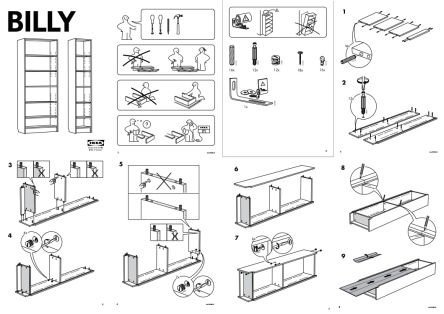
In het boek Het groot verbeterboek - meer dan 120 tools en concepten voor procesverbeteraars en verandermanagers beschrijven Neil Webers, Lucas van Engelen en Thom Luijben het Lean-instrument van de Standard Operating Procedure (SOP)::

Een SOP (Standard Operating Procedure) is een beschrijving van de standaardmanier van werken.
Resultaat
Het juiste gebruik van SOP's zorgt ervoor dat:
- Medewerkers duidelijk weten hoe zij hun werk op de meest effiiciënte manier kunnen uitvoeren;
- Medewerkers niet sneller, maar slimmer kunnen werken om hun doelstellingen te behalen;
- Medewerkers door training gemakkelijk multi-inzetbaar worden doordat zij meer SOP's beheersen;
- In combinatie met training de nieuwkomers sneller efficiënt inzetbaar zijn;
- Kwaliteit en veiligheid gegarandeerd worden
Aanpak
Een SOP moet zo worden opgesteld dat een persoon die totaal niets van de handeling afweet, aan de hand van die SOP de handeling zonder problemen op de meest efficiënte manier kan uitvoeren. Bij de meeste SOP's wordt er gewerkt met stappen en kernpunten, wat een simpel en bondig overzicht geeft. Verder worden ze geïllustreerd met foto's of tekeningen van de uit te voeren handeling. Volg deze stappen bij het opstellen van een SOP:
Stap-1
Bepaal het format van de basis-SOP-sjabloon. De kracht van standaardiseren van processen wordt mede bepaald door de vorm die je voor het standaardiseren kiest.
Stap-2
Bepaal voor welke processen en handelingen je een SOP wilt opstellen.
Stap-3
Bepaal wie de eigenaar wordt van welke SOP.
Stap-4
Houd een systematisch overzicht bij van alle SOP's, waarin je aangeeft of deze in ontwerp zijn of al geïmplementeerd zijn, welke versie de meest actuele is en wie de eigenaar is van elke SOP.
Stap-5
De eigenaar van elke SOP stelt deze op door eerst het procesonderdeel inclusief alle handelingen te observeren en te analyseren. Gebruik hiervoor checklisten en een stroomdiagram.
Stap-6
Laat de SOP beoordelen en controleren door iemand anders dan degene die hem heeft opgesteld. Bij voorkeur laat je deze persoon het proces uitvoeren met de SOP.
Stap-7
Implementeer de SOP. Bespreek de nieuwe of gewijzigde SOP's met de betrokken medewerkers voordat zij ze in gebruik nemen.
Stap-8
Wijzig een SOP als de procedure verandert of als het nodig is om de SOP te corrigeren of verduidelijken. Verander hierbij altijd het versienummer van de SOP en geef altijd aan wat de wijzigingen ten opzichte van de vorige versie zijn.
In de praktijk
Omdat er geregeld veranderingen plaatsvinden in een bedrijfsomgeving, is het essentieel dat de SOP up-to-date blijft. Want als een SOP niet meer up-to-date is, dan zal deze zeker niet gebruikt worden. Daarom moet een SOP geregeld gecontroleerd en aangepast worden. Bij het in gebruik nemen van de SOP moet dan ook het proces van SOP-aanpassingen goed worden georganiseerd en vastgelegd.
Valkuilen
Een SOP die niet wordt gebruikt, is verspilling. Sterker nog: als er wel SOP's zijn opgesteld, maar ze niet worden gebruikt, dan ontstaat er een cultuur waarin het prima is om je niet aan afspraken en standaarden te houden.
Bron: Het groot verbeterboek - meer dan 120 tools en concepten voor procesverbeteraars en verandermanagers, Neil Webers, Lucas van Engelen & Thom Luijben
Laatst aangepast op zaterdag, 02 december 2017 22:07
Jidoka volgens Rudy Gort (1)
Gepubliceerd in
Lean Six Sigma
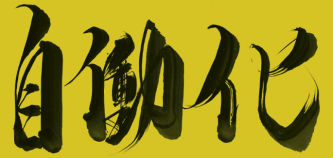
Rudy Gort beschrijft in zijn boek Lean Basis - fundament voor groei de herkomst van jidoka:

Kwaliteit inbouwen
Toen Sakichi Toyoda (1867-1930) eind negentiende eeuw opgroeide op het platteland, was het weven een belangrijke industrie. Knutselaar en uitvinder Sakichi leerde het timmermansambacht van zijn vader en gebruikte deze bekwaamheid om betere weefmachines te maken, die hij later motoriseerde. Aangezien onderdelen niet klant-en-klaar verkrijgbaar waren, moest hij de machine zelf proefondervindelijk werkend krijgen. Uiteindelijk werden zijn geautomatiseerde weefmachines zeer beroemd, vanwege een denkwijze die tot een slimmigheid leidde.
Het probleem van automatiseren is namelijk, dat wenneer er iets misgaat er al snel heel veel defecte producten gemaakt worden, die zich vervolgens opstapelen. Om dat te voorkomen ontwikkelde Sakici in 1896 een speicaal mechanisme om de weefmachine automatisch te stoppen zodra er een draadbreuk optrad. Zo werd voorkomen dat er fouten werden doorgegeven. Dit was tevens een bewustwordingssignaal dat er iets mis was (andon) en bij herhaling een grondige reden om de bronoorzaak op te sporen en maatregelen te nemen.
Deze denkwijze evolueerde naar een breder systeem dat één van de twee pijlers in Toyota's productiesysteem werd, genaamd, jidoka. In wezen betekent jidoka 'kwaliteit inbouwen in het proces', met technieken zoals poka-yoke ofwel ondoordringbaar voor fouten. Jidoka refereert tevens naar het dusdanig ontwerpen van processen en machines dat werknemers niet gebonden zijn aan de machine (autonomation), en daarmee vrijgemaakt zijn om waardetoevoegend werk te doen.
Van de verkoop van de patentrechten van zijn 'poka-yoke weefmachine' richtte Sakichi in 1937 de Toyota Motor Corporation op.
(...)
Sakichi zag dat de wereld veranderde. Auto's zouden de techniek van morgen worden, weefmachines de techniek van gisteren. Zijn zoon Kiichiro Toyoda (1894-1952) kreeg daarom de taak om de autobusiness op te bouwen. Hij leerde voor werktuigbouwkundig ingenieur - weliswaar op een universiteit, maar het vak leerde hij door te doen. De kennis van het maken van motoren kwam Kiichiro goed van pas. Hij bouwde voort op zijn vaders filosofie en managementaanpak, maar kwam ook met eigen innovaties. Hij bleef zich ontwikkelen en voerde in 1927 een productiemethode in op basis van een kettingtransportbaan naar de assemblagelijn van een textielfabriek. Zijn ideeën werden verder beïnvloed door een studiereis naar een Ford-fabriek in Michigan om de automobielindustrie te zien, en door Amerikaanse supermarkten betreffende het aanvullen van producten in de schappen wanneer ze verkocht waren.
Bron: Lean Basis - fundament voor groei, Rudy Gort
Laatst aangepast op zaterdag, 06 januari 2018 07:36
De Wet van Little volgens Webers, Van Engelen & Luijben
Gepubliceerd in
Lean Six Sigma
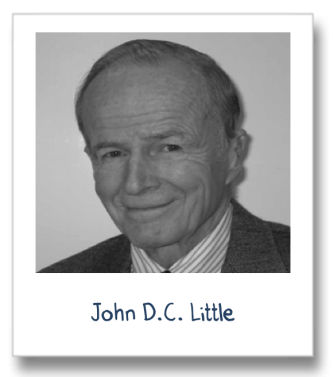
In het boek Het groot verbeterboek - meer dan 120 tools en concepten voor procesverbeteraars en verandermanagers beschrijven Neil Webers, Lucas van Engelen en Thom Luijben de Wet van Little:

De Wet van Little geeft inzicht in het effect van een verandering in een van de drie grootheden WIP, CT en GO op de andere twee.
WIP staat voor het Werk In het Proces. Dit zijn alle eenheden in het proces die uiteindelijk worden bewerkt tot een eindproduct. Bij diensten zijn dit de eenheden waaraan de dienst wordt geleverd.
CT staat voor CyclusTijd van de eenheid in het proces. Dit is de gemiddelde tijd in het proces die nodig is om een eenheid te produceren of van de dienst te voorzien. Dus de gemiddelde tijd dat de eenheden van begin tot eind in het proces zijn.
Go staat voor Gemiddelde Opbrengst: het aantal eenheden dat in het proces is geproduceerd per tijdseenheid.
De wet ziet er zo uit: WIP = CT * GO
Resultaat
De Wet van Little geeft inzicht in wat er gebeurt als je een van de drie grootheden in een proces verandert.
Aanpak
Er is geen sprake van een aanpak bij de Wet van Little waarbij het direct zichtbaar is dat het draaien aan één grootheid leidt tot het veranderen van één van de andere twee grootheden. In die zin is het geen gemakkelijke wet. Dit komt doordat deze grootheden onderling samenhangen. Het hangt helemaal af van de processituatie af (denk hierbij aan de capaciteit van de procesonderdelen, de tijd, de voorraden en de variatie in de procesprestaties en aanvoer) hoe de verandering in een van de grootheden leidt tot veranderingen in de andere twee. Zo zal het instellen van een bovengrens aan de WIP (wat de kern is van een kanban-systeem) betekenen dat de cyclustijd verlaagd moet worden om te voorkomen dat het gemiddeld geproduceerde aantal stuks achteruitgaat.
In de praktijk
In de praktijk geeft de wet bijvoorbeeld het volgende inzicht. (...) Mensen vinden het vaak onprettig om te werken tussen dossiers die nog in bewerking zijn. Uit analyses blijkt dat deze dossiers veelal 'wachtend' doorbrengen. Er is dus sprake van hoge WIP en een lange doorlooptijd. Het verminderen van de wachttijd van de dossiers (bijvoorbeeld door deze in één keer af te werken) vermindert de doorlooptijd en de dossiers zullen als sneeuw voor de zon uit het proces verdwijnen zonder dat de feitelijke productiviteit (de tijd waaraan werkelijk aan de dossiers wordt gewerkt) wordt verhoogd. En dat komt de werkbeleving ten goede.
Bron: Het groot verbeterboek - meer dan 120 tools en concepten voor procesverbeteraars en verandermanagers, Neil Webers, Lucas van Engelen & Thom Luijben
Laatst aangepast op zaterdag, 02 december 2017 22:07
Destructieve doelen volgens W. Edwards Deming
Gepubliceerd in
Lean Six Sigma

People with targets and jobs dependent upon meeting them will probably meet the targets - even if they have to destroy the enterprise to do it.
W. Edwards Deming
Laatst aangepast op zaterdag, 02 december 2017 22:08
Jidoka volgens John Shook & Toshiko Narusawa
Gepubliceerd in
Lean Six Sigma
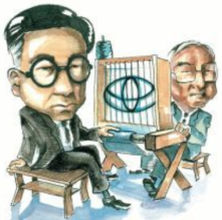
John Shook en Toshika Narusawa beschrijven in hun boek Kaizen Express - De bouwstenen voor jouw Lean traject het Lean-concept Jidoka:

Wat is Jidoka?
Jidoka of automatisering met een menselijk aspect
Jidoka [is één van de pilaren van TPS] De Japanse term 'jidoka' gebruiken we in elke taal als een technische TPS-term. In het Nederlands worden soms ook de termen 'intelligente automatisering', of 'automatisering met een menselijk aspec' of 'autonomisering' (een samenvoeging van 'autonome automatisering').
Jidoka heeft twee belangrijke kenmerken:
(1) Een automatische stop en (2) een waarschuwingssignaal. Maar het heeft ook een andere cruciale dimensie: het scheiden van mensen werk en machinaal werk en zorgen dat machines (of welke hulpmiddelen ook, inclusief software) voor mensen werken en niet andersom. Jidoka heeft betrekking op werkzaamheden met een ingebouwd vermogen om afwijkingen te signaleren en zichzelf stop te zetten om de productie van defecten te voorkomen.
Wat is Jidoka?
Jidoka betekent dat operators en apparatuur het vermogen hebben om te signaleren wanneer er een afwijkende situatie optreedt en direct het werk stil te leggen om maatregelen te nemen.
Waarom moeten we Jidoka werken?
Waar machines en processen zichzelf niet met Jidoka kunnen uitrusten, zijn er operators nodig om toezicht te houden op de apparatuur en defecten te voorkomen. Jidoka geeft operators het vermogen om in elk proces kwaliteit in te bouwen en om mensen te scheiden van machines om efficiënter te kunnen werken.
Wat kunnen we bereiken door mensenwerk van machinaal werk te scheiden?
Als operators met behulp van jidoka worden vrijgesteld van puur toezicht houden op machines, kunnen zij tijdens een machinecyclus ander waardecreërend werk doen.
(...)
Sakichi Toyoda (1867-1930), de oprichter van de Toyota Group, ontwikkelde het concept jidoka, aan het begin van de 20ste eeuw. (...) Toyoda vond een automatisch weefgetouw vond een automatisch weefgetouw uit dat zichzelf stopte als er problemen waren. In zijn weefgetouw bouwde hij het vermogen in om te stoppen zodra er een kettingdraad brak,, en om bijna lege spoelen uit te werpen en nieuwe in te brengen in de laatste seconde voordat een spoel volledig leeg was. Dit gebeurde allemaal terwijl de machine op volle snelheid draaide. Zijn uitvinding leidde tot grote kwaliteits- en productiviteitsverbeteringen en stelde operators in staat om werk te doen dat meer waarde opleverde dan simpelweg toezicht houden op automatische weefgetouwen.
Uiteindelijk werd dit concept - het zodanig ontwerpen van machines dat zij automatisch stopten en direct de aandacht vestigden op problemen - een cruciaal onderdeel van elke machine, elke productielijn en elke Toyota-activiteit.
(...)
Nog even terug naar jidoka
Jidoka betekent dat je ervoor zorgt dat een productieproces automatisch en direct stopt zodra er een probleem of defect optreedt. De vroegste vorm van jidoka werd in de jaren twintig van de vorige eeuw uitgevonden door Sakichi Toyoda, die het toepaste voor zijn automatische weefgetouwen.
Bron: Kaizen Express - De bouwstenen voor jouw Lean traject, Toshiko Narusawa & John Shook
Laatst aangepast op zaterdag, 02 december 2017 22:07
Ingebouwde kwaliteit (Jidoka) volgens Rudy Gort
Gepubliceerd in
Lean Six Sigma
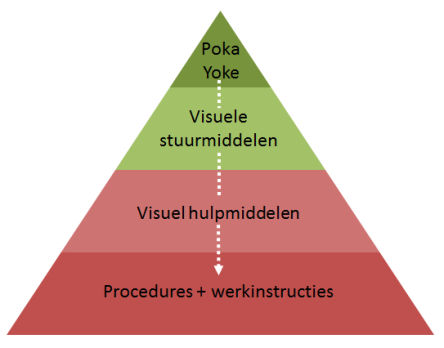
Rudy Gort beschrijft in zijn boek Lean Basis - fundament voor groei hoe Lean streeft naar het inbouwen van kwaliteit in het proces:

Jidoka: kwaliteit ingebouwd
Jidoka ... gaat over het kwaliteit inbouwen in het proces. Het verwijst naar de eigenschap om afwijkingen te detecteren en te stoppen, zodat er geen fouten worden geproduceerd en doorgegeven.
(...)
Het Jidoka-principe gaat helemaal terug tot Toyota-oprichter Sakichi Toyoda, met zijn uitvinding van de automatische weefmachines. Een van zijn uitvindingen was een hulpmiddel dat een draadbreuk kon detecteren (door een loodje aan het draadje at op de grond viel na een draadbreuk) en de machine direct stopte. Het belangrijke hieraan was dat men de mogelijkheid had het probleem op te lossen en verdere kwaliteitsproblemen te voorkomen. Een simpel idee dat leidde tot diepgaande inzichten: kwaliteit moet ingebouwd worden tijdens het proces, omdat achteraf te laat is. Hiervoor is wel vereist dat de macht wordt teruggegeven aan de medewerkers en ze doorlopend gestimuleerd worden deze empowerment daadwerkelijk te gebruiken.
Voorkomen is beter
Kwaliteit verbeteren door eindinspectie is te laat, ineffectief en kostbaar. Wanneer een product eenmaal de fabriek heeft verlaten, is het te laat om er nog iets aan te doen. En je krijgt geen kwaliteit door inspectie, maar door verbetering van het productieproces. Inspectie, afkeuren, afwaarderen en herstelwerk zijn geen corrigerende acties op het proces. Herstelwerk verhoogt kosten en niemand vindt het leuk werk. Het aantal inspecteurs verhogen helpt al helemaal niet en werkt zelfs averechts, omdat elke inspecteur ervan uitgaat dat de ander zijn werk doet en dus heeft geïnspecteerd. Kwaliteitsinitiatieven door inspectie laten een oppervlakkige toewijding aan kwaliteit zijn, het geeft mensen hooguit het gevóél dat ze iets bereikt hebben. Bovendien zorgt continue inspectie voor een angstcultuur, waarbij tegenspraak wordt gelabeld als 'anti-kwaliteit'.
Ingebouwde kwaliteit - zorgen dat problemen niet verder doorgeschoven worden - is veel effectiever en minder duur dan inspecties en reparaties van kwaliteitsproblemen aan het einde van de lijn. Het belang van 'in één keer goed' en 'geef geen fouten door' neem daardoor sterk toe. Je wordt in een lean-organisatie dan ook niet bekritiseerd wanneer je kwaliteit vooropstelt en zodoende productiedoelstellingen niet haalt; maar wel wanneer je problemen niet meldt. Het is binnen een Lean-systeem namelijk van groot belang dat je tijdig de hulpvraag stelt (door een andon-signaal te geven) en de bronoorzaak achterhaalt en oplost.
(...)
[Door] de druk om 'de getallen' te halen wordt dit de gewoonte. Foutieve indicatoren en beloning op getallen (output) in plaats van gedrag (proces), maakt van elke trotse kwaliteitsmedewerker een afgestompte doordouwer. Een kwaliteitsverbeterprogramma heeft dan ook weinig zin wanneer het niet vergezeld gaat met aanpassingen in prikkels (persoonlijke bonussen), wervingsbeleid, productstrategie en budgetteringspraktijken.
Fouten worden eenmaal gemaakt, maar we kunnen ze stoppen voordat ze doorgaan naar het volgende proces! In lean-termen heet dit zone control. Bij traditionele inspectie wordt een gespecialiseerde kwaliteitscontroleur van buiten het werkproces gebruikt. Bij lean zone control daarentegen, zoekt men naar methoden om fouten te voorkomen, of ervoor te zorgen dat we ze niet doorgeven. Want problemen oplossen bij de bron bespaart uiteindelijk verderop tijd en geld. Daarom is Toyota zoveel succesvoller dan andere organisaties, omdat het sterk is in het eerder zien van problemen. Niet pas wanneer deze groot zijn, maar wanneer ze klein en overzichtelijk zijn, eenvoudig te begrijpen en er nog iets aan te doen is.
Wat veel gebeurt om fouten te voorkomen, is procedures schrijven. Echter, papier is geduldig en procedures worden zelden gelezen of onthouden, en voorkomen daarmee nauwelijks fouten. Sterker nog, ze verhogen slechts de werklast waardoor de kans op fouten toeneemt! Denk maar eens aan een spoorwegovergang. Je kunt een bord met tekst plaatsen, maar dan gaat het ooit een keer vreselijk mis (wat dus ook te vaak gebeurt). Daarom gaan we het liefst boven in de zogenoemde borgingspiramide zitten. Zoeken naar een slimme manier om fouten te voorkomen, zodat je geen fouten kunt maken. Dit noemt men poka yoke middelen, ook wel het fool-proof maken. Het zijn veelal simpele en creatieve, maar zeer effectieve oplossingen (denk maar aan het loodje aan het weefdraad). Hierbij hoort ook een standaard, die zegt wat er moet gebeuren als er een afwijking wordt gevonden. Standaardisatie - en de visualisatie daarvan - is zelf ook een manier om kwaliteitsproblemen te voorkomen.
Een goede manier om fouten te voorkomen voldoet aan de volgende criteria:
- het is simpel, gaat lang mee en vereist weinig onderhoud;
- het heeft een hoge betrouwbaarheid
- het is ontworpen voor de werkpleksituatie
- het is goedkoop
Geef empowerment
In de tijd van het ambacht lag de kwaliteitscontrole geheel bij degene die het product maakte. Toen we meer in massa zijn gaan produceren, werden uitvoering en denkwerk - en daarmee de verantwoordelijkheid voor kwaliteit - gescheiden (met 'dank' aan Henri Fayol). Kwaliteitssystemen zoals ISO-9001 hebben hier geen echte verandering in gebracht. De meeste bedrijven leggen de verantwoordelijkheid in dat geval bij een stafafdeling en controleren met (twee)jaarlijkse audits of de regeltjes worden gevolgd. De verleiding is groot om te leunen op stapels bureaucratische documentatie, zonder dat de klant er beter van wordt. Verwar kwaliteit en standaardisatie binnen Lean dus niet met bureaucratische systemen zoals ISO-9001, die gebruikt worden als een gedetailleerd handboek met vastgeroeste standaardprocedures die gevolgd moeten worden, of met kwaliteitsafdelingen die met statische analysemethodes een grote stroom data analyseren, zoals bij Six Sigma.
Binnen Lean ligt de verantwoordelijkheid voor kwaliteit bij degene die het proces uitvoert. Met machines kunnen we weliswaar iets inbouwen waardoor ze automatisch afwijkingen detecteren en stoppen, maar hoe doen we dat met mensen? Dat kan door ieder teamlid de verantwoordelijkheid én morele verplichting te geven om, zodra er een afwijking van de standaard is, het proces stil te laten leggen (door op een knop te drukken of aan een koord te trekken). Ze voelen dan de macht, echte empowerment, en weten daarmee ook dat ze serieus genomen wordt. (...) Het werkt volgens Jeffrey Liker alleen wanneer je de werknemers het principe duidelijk maakt van het 'aan de oppervlakte brengen van kwaliteitsproblemen', zodat ze deze problemen in het vervolg kunnen verhelpen en voorkomen. Teamleiders moeten bereikbaar zijn; stand-by staan voor als er een hulpsignaal i.
(...)
Het blijkt overigens moeilijk dit principe over te brengen, omdat de veronderstelling bij medewerkers leeft dat ze verweten worden van slecht werk wanneer ze een stopsignaal moeten geven. De mores is immers: het maakt niet uit hoe je dat doet, zolang je maar de afgesproken aantallen haalt! Het beruchte management by numbers. Te veel productie is onder zo'n regime geen probleem, maar bij te weinig krijg je de wind van voren. Kwaliteitsproblemen worden dan gewoon uit de lijn gehaald, zodat men maar door kan gaan. Deze probleemgevallen worden later wel bekeken, door een speciale afdeling. Het duurt zodoende vaak maanden om iemand bij te brengen dat het een must is om een stopsignaal te geven bij problemen.
Bron: Lean Basis - fundament voor groei, Rudy Gort
Bewaren
Laatst aangepast op maandag, 23 oktober 2017 18:53
Lean volgens Stassen, Torremans & Van der velde (2)
Gepubliceerd in
Lean Six Sigma
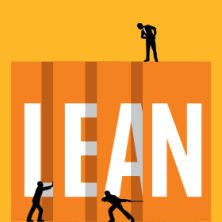
Ruud Stassen, Huub Torremans & Bas van der Velde visualiseren in het artikel Lean-INK: continu en cyclisch verbeteren beschrijven Lean management als volgt:

Lean management is gebaseerd op de manier waarop een organisatie haar processen inricht, bestuurt en verbetert en vindt zijn oorsprong in het Toyota Productie Systeem (TPS). Belangrijke uitgangspunten daarbij zijn maximaliseren van klantwaarde en het elimineren van verspilling. De Lean management-benadering bestaat uit een groot aantal bouwstenen en instrumenten, ingebed in een heldere managementfilosofie. Lean management kent daarbij drie pijlers:
-
Lean leiderschap (Lean leading): 'Lean leiderschap' stelt eisen aan het management. In de kern ooit goed samengevat als 'Go see, Ask why, Respect your people' .
-
Lean denken (Lean thinking): 'Lean denken' betekent begrijpen hoe het proces in haar geheel (het systeem) werkt voordat je ingrijpt.
-
Lean instrumenten (Lean tooling): 'Lean instrumenten' betekent vooral het gebruiken van verstoringen en verspillingen zichtbaar te maken en vervolgens het proces van continu verbeteren waarin medewerkers en management deze 'problemen' structureel oplossen.
(...)
Bij Lean management vormen de 'tools' misschien wel het meest tastbare, maar niet het meest fundamentele onderdeel. De tools die binnen Lean management gebruikt worden, leiden pas echt tot duurzame organisatieverbetering als de organisatie zich de manier van denken eigen heeft gemaakt en als de leiding actief Lean management uitdraagt.
Bron: Lean-INK: continu en cyclisch verbeteren, Ruud Stassen, Huub Torremans & Bas van der Velde; in: Kwaliteit in Bedrijf (oktober 2010)
Laatst aangepast op zaterdag, 02 december 2017 08:42
|