Six Sigma: voorspelbare prestaties
Gepubliceerd in
Lean Six Sigma
Laatst aangepast op donderdag, 11 januari 2018 19:40
Doorlooptijd(vermindering) volgens Tim de Wit
Gepubliceerd in
Lean Six Sigma
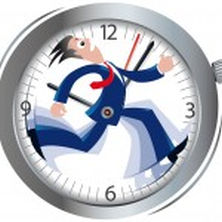
In zijn bachelorscriptie Technische Bedrijfskunde gaat Tim de Wit in op de theorie van doorlooptijd en doorlooptijdverkorting:

De doorlooptijd van een product (Engels: lead time of cycle time, beide termen worden ook gebruikt om andere begrippen aan te duiden) wordt gedefiniëerd als de tijd die een product erover doet om een proces geheel te doorlopen (Rother & Shook, 1999) en kan worden gemeten door de begintijd van het proces te vergelijken met de eindtijd van het proces – meestal de levering aan de klant.
(...)
Een lagere doorlooptijd heeft namelijk een gunstige invloed op het bedrijf op meerdere manieren (Hopp, Spearman, & Woodruff, Practical Strategies for Lead Time Reduction, 1990):
- Bestellingen kunnen sneller geleverd worden aan klanten;
- Er hoeven minder voorspellingen te worden gedaan over toekomstige vraag;
- Er is minder voorraad tussen bewerkingsstappen;
- Eventuele productiefouten komen sneller bij de kwaliteitscontrole en worden dus sneller opgemerkt;
- Er is beter overzicht omdat er minder producten op de vloer staan.
Het staat dus vast dat een lage doorlooptijd wenselijk is voor productiebedrijven. Uit de wet van Little blijkt ook op welke manier dit te bereiken is. Om dit te illustreren, is de vergelijking omgeschreven naar een andere vorm:
Onderhanden werk (work in process; WIP) = doorlooptijd x productiesnelheid óf Productiesnelheid = WIP / Doorlooptijd
Uit deze vergelijking blijkt dat de verhouding tussen voorraad onderhanden werk en het aantal geproduceerde producten per tijdseenheid, gelijk is aan de gemiddelde doorlooptijd. Deze doorlooptijd kan dus worden verlaagd of verhoogd door aanpassingen aan de andere twee variabelen. De voorraad onderhanden werk verminderen zonder hierbij de productie te verlagen zou zo de gemiddelde doorlooptijd verminderen.
De doorlooptijd van een enkel product is als volgt opgebouwd (Hopp, Spearman, & Woodruff, Practical Strategies for Lead Time Reduction, 1990):
Doorlooptijd = bewerkingstijd + omsteltijd + transporttijd + bufferwachttijd + onderdelen wachttijd + batchwachttijd
Het verkorten van de genoemde bewerkingsen wachttijden betekent ook het verkorten van de totale doorlooptijd. Voor elke tijd zal nu worden uitgelegd hoe deze gedefinieerd wordt en hoe deze van invloed is op de doorlooptijd van producten.
Bewerkingstijd: de tijd waarin een product wordt bewerkt op de verschillende machines of werkplekken om er waarde aan toe te voegen. In de meeste fabrieken is de bewerkingstijd slechts een zeer klein deel van de gehele doorlooptijd (Rother & Shook, 1999). Het verkorten van de bewerkingstijd verhoogt de capaciteit van het productieproces, wat bij gelijkblijvende voorraad onderhanden werk zorgt voor een verlaging van de doorlooptijd.
Omsteltijd: de tijd die nodig is om de machines of werkplekken klaar te maken om een productiebatch te bewerken. Met omsteltijd wordt in dit geval interne omsteltijd bedoeld: hierbij geldt dat machines tijdens het omstellen geen bewerkingen kunnen uitvoeren en dus geen waarde toevoegen aan producten. Kortere omsteltijden zorgen ervoor dat machines dezelfde bezettingsgraad kunnen halen met kleinere batchgroottes, wat een gunstige invloed heeft op de batchwachttijd. Dit betekent dat een gelijke capaciteit kan worden gehaald met een lagere voorraad onder handen werk, wat zorgt voor een vermindering van de doorlooptijd.
Transporttijd: de tijd waarin een product binnen het productieproces wordt verplaatst, bijvoorbeeld van de ene machine naar de andere. Het verlagen van de transporttijd maakt het mogelijk om met minder voorraad in de fabriek dezelfde capaciteit te halen. Hierdoor wordt de doorlooptijd verlaagd.
Bufferwachttijd: de tijd waarin een product als buffervoorraad ligt te wachten voor een machine. Buffervoorraad is een voorraad die voor een machine wordt opgebouwd om ervoor te zorgen dat de machine kan doorwerken als de machine ervoor om wat voor reden dan ook niet op tijd nieuwe producten levert. De bufferwachttijd kan verminderd worden door het verminderen van de voorraad onderhanden werk in het systeem. De buffervoorraden in het hele systeem zullen dan kleiner worden en de doorlooptijd wordt verminderd. Als de buffervoorraden echter te laag worden, kan dat in onvoorspelbare systemen leiden tot onnodige stilstand van machines.
Onderdelenwachttijd: deze wachttijd ervaart een product als het moet wachten op onderdelen uit een ander proces die nog niet geleverd zijn, bijvoorbeeld vanwege een kapotte machine of een slechte planning. Er kan dan niet verder worden gewerkt aan het product. Als er geen buffervoorraad is om de uitval op te vangen, kan deze wachttijd leiden tot een tijdelijke vermindering van de capaciteit, wat leidt tot een langere doorlooptijd. In principe komt deze wachttijd alleen voor als zich incidenten voordoen.
Batchwachttijd: de tijd die een product moet wachten op de andere producten in dezelfde batch. Deze tijd is gelijk aan de totale bewerkingstijd van een batch minus de bewerkingstijd van één product. Deze wachttijd kan worden verminderd door het aantal producten in een batch te verlagen. Hiermee kan de doorlooptijd worden verlaagd, maar alleen als de omsteltijd hier laag genoeg voor is. Als dit het geval is, wordt de doorlooptijd korter vanwege een lagere voorraad voor dezelfde capaciteit.
Duidelijk is dat de indeling van het productieproces in combinatie met de capaciteit van het proces de doorlooptijd bepaalt. Als er wordt gewerkt met grote batches en lange omsteltijden is voor een hoge capaciteit een langere doorlooptijd nodig dan wanneer er wordt gewerkt met kleine batches en kortere omsteltijden.
BEPALENDE EIGENSCHAPPEN
Nu bekend is uit elke soorten wacht- en bewerkingstijden de doorlooptijd is opgebouwd, kan worden onderzocht welke factoren de doorlooptijd beïnvloeden. Het is duidelijk dat een maatregel om de doorlooptijd te verkorten, de verhouding tussen productiecapaciteit en voorraad onderhanden werk zó moet veranderen, dat de voorraad lager wordt ten opzichte van de capaciteit.
Er zijn twee eigenschappen van productieprocessen die een sterk effect hebben op de doorlooptijd van producten (Krajewski, King, Ritzman, & Wong, 1987):
Batchgrootte: deze variabele is direct van invloed op de batchwachttijd van producten. Hoe groter de batch, des te langer producten moeten wachten om naar de volgende bewerking moeten gaan. In sommige processen worden productiebatches in meerdere kleine transportbatches naar de volgende machine vervoerd; in deze gevallen geldt de grootte van de transportbatch. Kleinere batches zorgen over het algemeen voor minder batchwachttijd, maar verhogen de hoeveelheid omstellingen die moet worden gedaan.
Omsteltijd: de tijd die nodig is om een machine van de ene bewerking over te schakelen naar het doen van een andere bewerking. De omsteltijd is bepalend voor het gelijknamige deel van de doorlooptijd, dat eerder besproken is. Lagere omsteltijden zorgen over het algemeen voor lagere doorlooptijden.
Belangrijk is wel dat de fabriek zich als doel heeft gesteld om de doorlooptijd te verlagen en hiervoor aanpassingen heeft gedaan. De auteurs stellen dat de doorlooptijd van een fabriek voor een groot deel afhankelijk is van deze twee variabelen. Verder is het een groot voordeel als in de fabriek gestreefd wordt naar het verlagen van doorlooptijden en het beheersen van de voorraad. Hiervoor zijn verschillende productiecontrolesystemen beschikbaar, die allemaal goed werken in bepaalde situaties. Welk systeem het beste werkt, is vooral afhankelijk van de inrichting van het productieproces, productvariatie, flexibiliteit van de werknemers en de twee bovengenoemde variabelen (Krajewski, King, Ritzman, & Wong, 1987).
Bron: Doorlooptijdreducte door werklastbeheersing binnen een Nederlandse leerlooierij (Bachelorscriptie Technische Bedrijfskunde), Tim de Wit
Laatst aangepast op donderdag, 04 januari 2018 06:04
Continu verbeteren met DMAIC
Gepubliceerd in
Lean Six Sigma
Laatst aangepast op dinsdag, 24 oktober 2017 07:06
Doorlooptijd als ultieme kpi volgens Marcel van Assen
Gepubliceerd in
Lean Six Sigma
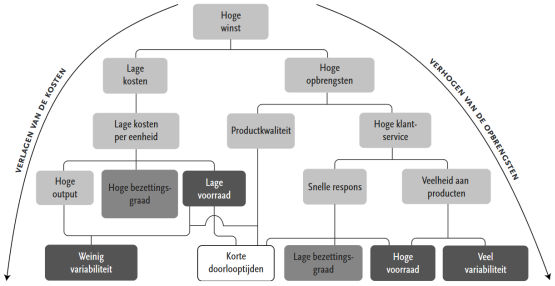
In het boek Operational Excellence beschrijft Marcel van Assen hoe hij doorlooptijd ziet als dé ultieme kpi:

Doorlooptijdverkorting als ultieme kpi
Operational Excellence als aanpak om de kosten te verlagen (ofwel het verhogen van de doelmatigheid en efficiëntie) en tevens de opbrengsten te verhogen (ofwel het verhogen van de doeltreffendheid en effectiviteit) leidt binnen de operationele organisatie tot diverse spanningen. Vanuit efficiëntie-oogpunt is een hoge bezetting van de bedrijfsmiddelen gewenst, weinig voorraad en een beperkte productmix (weinig variatie), terwijl vanuit een verkoopperspectief juist een brede productmix (veel variatie), veel voorraad en een lage bezetting gewenst is om een snelle respons en een hoge customer-service te garanderen.
Het streven naar een doeltreffende en doelmatige operationele bedrijfsvoering vertaalt zich dus in diverse (ogenschijnlijke) tegenstrijdigheden. Om een operationeel excellente organisatie te ontwikkelen, volstaat het louter nemen van efficiëntiemaatregelen niet meer. Organisaties die daar toch voor kiezen, zijn continu bezig met het blussen van operationele branden, waardoor ze geen tijd hebben voor een proactieve benadering van de markt. Operational Excellence vereist een moderner perspectief, waarin tijd (snelheid) centraal staat en doorlooptijdverkorting de ultieme prestatie-indicator is.
Doorlooptijdverkorting, of beter het idee van snelheid als concurrentievoordeel (Stalk & Hout, 1990), ontstond begin jaren negentig als gevolg van de Japanse ontwikkelingen rondom het Just-in-time-principe. Niet alleen gaat het erom precies op tijd te leveren (op het juiste moment), maar ook om het product of de service in zo weinig mogelijk tijd te maken en te leveren, ofwel met korte doorlooptijden. Het hebben van korte doorlooptijden werkt positief door op leverbetrouwbaarheid, klantenservice en efficiëntie.
Voor veel managers is dit echter niet zo evident. Als hun gevraagd wordt hoe ze honderd procent leverbetrouwbaarheid kunnen garanderen, ongeacht de onzekerheid in de klantvraag (volume en tijdstip), dan kiezen managers er in het algemeen voor om (oneindig veel) voorraad aan te houden van alle mogelijke producten die ze willen kunnen leveren. Ze hadden er ook voor kunnen kiezen om elk product in een oneindig korte doorlooptijd te kunnen maken en leveren, zodat alle vraag direct op klantspecificatie gemaakt en geleverd kan worden. Natuurlijk is het realiseren van een oneindig korte doorlooptijd een utopie, maar het aanhouden van oneindig veel voorraad is evenzeer kostbaar (en voor de meeste dienstverleners ook onmogelijk). Overigens betekent een oneindig korte interne doorlooptijd dat er nauwelijks directe kosten hoeven te worden gemaakt voor het produceren en leveren van het product of dienst. Het gaat hier natuurlijk om de gedachtegang: als het vermogen van een korte doorlooptijd kan worden verkregen tegen acceptabele investeringen, dan leidt het altijd tot de meest efficiënte bedrijfsvoering.
Snelheid (en dus doorlooptijdverkorting ) heeft direct te maken met flexibiliteit en betrouwbaarheid. Hoe sneller een organisatie kan omschakelen, hoe flexibeler ze is. Voor het opbouwen van dit vermogen zijn natuurlijk investeringen nodig, maar dan vooral in aandacht en tijd, om een cultuur van continu verbeteren en slimmer werken te creëren (zodat niet-waardetoevoegende tijd wordt geëlimineerd). Toch kiezen veel productieorganisaties en dienstverleners bij het afspreken van levertijden ervoor om wat speling in te bouwen om eventuele verstoringen te kunnen opvangen. Ze buff eren de onzekerheid met extra (doorloop)tijd; daarmee proberen ze een meer betrouwbare leverancier te zijn. Er is echter geen garantie dat het afspreken van langere levertijden meer betrouwbaarheid oplevert, omdat er met langere levertijden juist meer kans op verstoring is, zoals een spoedorder of een machinestoring. Dergelijke verstoringen verlengen juist de doorlooptijd. Andersom geldt: hoe korter de doorlooptijd, hoe kleiner de kans op verstoringen binnen de doorlooptijd, en hoe hoger de leverbetrouwbaarheid. Het hebben van korte doorlooptijden heeft ook een positieve invloed op de voorraadniveaus (van eindproducten en van het onderhanden werk), op de kwaliteit van de producten en diensten, en op de responssnelheid naar klanten toe.
Doorlooptijdverkorting is een middel om gelijktijdig aan meerdere andere prestatie-indicatoren te voldoen. Immers, de kwaliteit moet hoger zijn omdat snelheid alleen bereikt kan worden als dingen direct goed gedaan worden. Daarbij zal de betrouwbaarheid van de bedrijfsmiddelen ook hoger (moeten) zijn. Met andere woorden, doorlooptijdverkorting impliceert hogere kwaliteit, grotere betrouwbaarheid en hogere flexibiliteit; het is het mechanisme bij uitstek om efficiëntie en productiviteit te verhogen.
Bron: Operational Excellence - van industrie tot dienstverlening, Marcel F. van Assen
Laatst aangepast op donderdag, 04 januari 2018 05:54
Lean: eliminate waste
Gepubliceerd in
Lean Six Sigma
Laatst aangepast op dinsdag, 20 februari 2018 07:20
Prestatie-indicatoren volgens Marc Muntinga & Niels Lagerveld
Gepubliceerd in
Lean Six Sigma
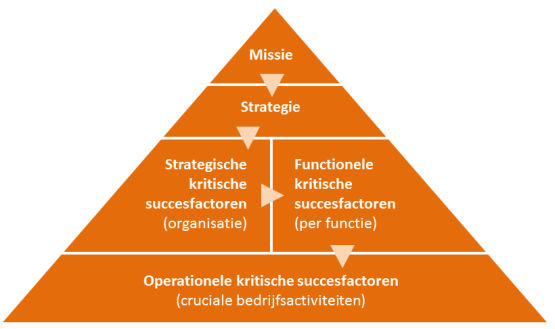
Marc A. Muntinga & Niels J. Lagerveld gaan in hun boek Managementmodellen voor kwaliteit in hoe prestatie-indicatoren ingezet kunnen helpen bij het besturen van een organisatie:

Prestatie-indicatoren worden ontwikkeld om organisaties beter te besturen, of in ieder geval om over betere informatie te beschikken met behulp waarvan de organisatie eenvoudiger is te besturen. Het is van groot belang over structurele informatie te beschikken die inzicht geeft over hoe de stand van zaken is bij de verschillende cruciale bedrijfsactiviteiten. Loopt alles volgens plan of zijn er afwijkende situaties waarop actie moet worden ondernomen? Een organisatie kan haar prestaties volgen door het ontwikkelen van factoren die van essentieel belang zijn voor de continuïteit en die vervolgens meetbaar te maken.
(...)
Prestatie-indicatoren
Prestatie-indicatoren zijn kwantitatieve gegevens die indicaties geven over de prestaties van een bepaald proces. De gemeten prestaties worden afgezet tegen normen op basis waarvan wordt vastgesteld of bij afwijkingen actie moet worden ondernomen.
Kritische succesfactoren
Kritische succesfactoren zijn voorwaarden die van doorslaggevende betekenis zijn voor het realiseren van de doelstellingen van een organisatie.
(...)
Het [proces van het ontwikkelen van presatie-indicatoren] begint met het formuleren van de missie en de strategie. De missie is de 'raison d'être' van een organisatie. Het (top)management dient in de missie in kwalitatieve termen kort en krachtig te formuleren wat de organisatie wil bereiken. Hoe de missie moet worden gerealiseerd, staat beschreven in de strategie. Een manier om tussentijds inzicht te hebben in de mate waarin de strategie wordt gerealiseerd, is het benoemen van kritische elementen uit die strategie en deze meetbaar te maken met prestatie-indicatoren.
De kritische succesfactoren vormen dus het uitgangspunt voor de ontwikkeling van prestatie-indicatoren. De basis voor de ontwikkeling van de kritische succesfactoren wordt op haar beurt weer gevormd door de missie en de strategie. De kritische succesfactoren zijn die gebieden waarin het behalen van goede prestaties een noodzakelijke voorwaarde vormt voor het realiseren van de doelstellingen van een organisatie. Ze geven een kwalitatief antwoord op de vraag die van groot belang is voor het management: 'Op welke terreinen kunnen we succesvol zijn en blijven, met andere woorden hoe kan de organisatie concurrentievoordelen realiseren en handhaven.' Het accent wordt in de organisatie gelegd op deze kritische gebieden en dus niet op de gebieden die minder belangrijk zijn voor het realiseren van de doelstellingen. Deze bijzaken krijgen geen plaats in de managementrapportage.
Het verband tussen missie, strategie, kritische succesfactoren en prestatie-indicatoren kan schematisch worden weergegeven in de kritische-succesfactorenpiramide. [Muntinga en Lagerveld] onderscheiden drie soorten kritische succesfactoren:
-
Strategische kritische succesfactoren.
-
Functionele kritische succesfactoren.
-
Operationele kritische succesfactoren.
De strategische kritische succesfactoren zijn cruciaal voor de continuïteit van de gehele organisatie, de functionele kritische succesfactoren zijn ondersteunend aan het succesvol uitvoeren van de strategie. En de operationele kritische succesfactoren ten slotte, zijn van groot belang voor het volgen van bedrijfsactiviteiten die altijd goed moeten worden uitgevoerd. Dit zijn zoals gezegd, de zogenaamde cruciale bedrijfsactiviteiten.
(...)
[Muntinga en Lagerveld] onderscheiden drie criteria waarop activiteiten en processen in organisaties kunnen worden gemeten:
-
(Doorloop)tijd: de doorlooptijd is van belang voor het beoordelen van processen, enerzijds omdat de doorlooptijd een maatstaf kan zijn voor de effectiviteit van het proces en anderzijds omdat een indruk kan worden gekregen van de efficiëntie van datzelfde proces.
-
Kwaliteit (effectiviteit): de kwaliteit van processen kun je meten aan de throughput-kant en aan de output-kant. De organisatie en/of proceseigenaar krijgt dus een indruk over de uitvoering tijdens en de resultaten van het proces.
-
Productiviteit (efficiency): bij de productiviteit gaat het om de verhouding tussen de kosten van de input, volume of bijvoorbeeld kosten van de winst ten opzichte van een eenheid output van een bepaald proces. Het meten van de productiviteit van een proces komt het meest overeen met de metingen die geregistreerd staat in een financieel georiënteerd meetsysteem.
Hierna komen de criteria voor een goede prestatie-indicator aan bod:
-
De prestatie-indicator moet voor iedereen in de organisatie eenvoudig te begrijpen zijn.
-
Iedereen moet hetzelfde verstaan onder de gekozen definitie. De indicator moet dus eenduidig worden gedefinieerd.
-
De prestatie-indicator moet informatief zijn. Hij moet inzichtelijk zijn en in één oogopslag de stand van zaken weergeven.
-
De prestatie-indicator moet motiverend werken en beïnvloedbaar zijn. .
-
De indicator moet onderdeel zijn van het beleid en aansluiten bij de organisatiedoelstellingen of urgente kwaliteitsproblemen.
-
Het meten van de interne en externe klanttevredenheid, met als insteek verbeteracties te ondernemen als dat nodig blijkt, werkt bevorderend op de klantgerichtheid.
-
De prestatie-indicatoren moeten worden opgesteld met betrokkenen.
Bepalen van normen
Na het vaststellen van de prestatie-indicatoren moet worden nagegaan of de behaalde resultaten als goed kunnen worden beoordeeld. Er moeten normen worden gesteld. (...) Vaak is het niet direct mogelijk een norm aan een prestatie-indicator te koppelen. Eerst moet inzicht worden verkregen in het bepalen van 'zinvolle' normen. Een zinvolle normstelling is alleen mogelijk als de betrokkenen ervan overtuigd zijn dat de norm eerlijk, reëel en haalbaar is. Is dit niet het geval dan leidt het stellen van normen tot frustratie.
Bron: Managementmodellen voor strategie en kwaliteit, Marc A. Muntinga & Niels J. Lagerveld
Bewaren
Laatst aangepast op zaterdag, 26 mei 2018 07:12
SIPOC volgens Marcel van Assen
Gepubliceerd in
Lean Six Sigma
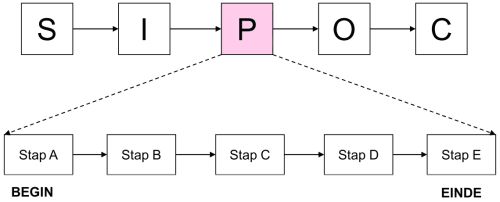
Marcel van Assen beschrijft in zijn boek Handboek Lean management het Lean-instrument van de SIPOC:

SIPOC staat voor Suppliers - Input - Process - Output - Customers, en is een techniek om een hoofdproces en het hele speelveld op hoofdlijnen te beschrijven, waarbij ook de input, de output, de klant(en) en de leverancier(s) van dat proces beschreven worden:
-
Identificeer en benoem het hoofdproces.
-
Bepaal duidelijk het startpunt en het eindpunt van het proces.
-
Kijk voor het hele hoofdproces welke output en klanten hierbij betrokken zijn. Identificeer de eisen van alle output (gezien vanuit de klant).
-
Vertaal het hoofdproces in enkele (maximaal vijf) hoofdprocesstappen.
-
Identificeer voor het hoofdproces de (belangrijkste) input en leveranciers (suppliers).
-
Afronden van de SIPOC: evalueer alle informatie en verifieer of alle essentiële onderwerpen zijn benoemd.
Bij (5) geldt dat het in de praktijk steeds vaker voorkomt dat men voor elke processtap van een hoofdproces bepaalt wat de output is en wie de klanten zijn. In ieder geval dient de output bekeken te worden vanuit het oogpunt van de klant en moet er worden geïdentificeerd welke eisen klanten stellen aan de door hun verlangde output. Ook bij (6) geldt dat steeds vaker voor elke processtap wordt bepaald wat de input is en welke toeleveranciers daarvoor nodig zijn. Definieer waaraan de input precies moet voldoen. Let hierbij niet alleen op de eisen van de leveranciers, maar ook op die van de ontvanger die de input nodig heeft.
Bron: Handboek Lean management - aanpak, concepten en modellen voor het succesvol toepassen van Lean, Marcel van Assen
Laatst aangepast op zaterdag, 12 september 2020 15:16
5 x Waarom-methode volgens Ron Emmerik
Gepubliceerd in
Lean Six Sigma
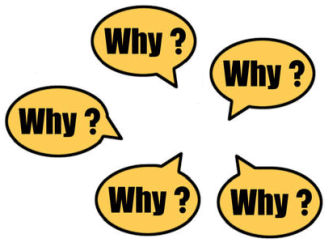
In het boek Kwaliteitsmanagement beschrijft Ron Emmerik de 5 x Waarom-methode:

Bij de 5 x Waarom-methode wordt steeds de waaromvraag gesteld, waardoor een dieper inzicht ontstaat in de werking van het proces. Door waaromvragen te stellen, wordt namelijk op een steeds dieper niveau nagedacht over wat in het proces allemaal een rol speelt, waarom activiteiten niet goed werken, waarom iets 'altijd' misgaat en wat de basismechanismen van het proces zijn. Dit biedt inzicht in de echte oorzaak van een probleem. Het stellen van waarom vragen geeft ook de mogelijkheid om als vanzelfsprekend beschouwde zaken weer bespreekbaar te maken. Pas de 5 x Waarom-methode toe bij verschillend medewerkers.
-
Formuleer op een begrijpelijke wijze het probleem door de vraag te stellen 'Waarom gebeurt dit?'
-
Stel de waaromvraag nogmaals op basis van het eerste antwoord.
-
Herhaal de waaromvraag daarna nog driemaal op basis van de gegeven antwoorden totdat de echte oorzaak boven water is gekomen.
De doelstellingen van de 5 x Waarom-methode is het analyseren van de problematiek en het leren van de gemaakte fouten.
Bron: Kwaliteitsmanagement, Ron Emmerik
Laatst aangepast op zaterdag, 02 februari 2019 16:35
Lean leiderschap volgens Marcel van Assen
Gepubliceerd in
Lean Six Sigma
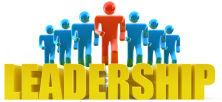
Marcel van Assen stelt in zijn boek Handboek Lean management dat leiderschap een belangrijke schakel is bij het succesvol realiseren van een Lean-organisatie.

[Het succes van Lean leiderschap] valt of staat met het zichtbare commitment van het topmanagement aan Lean. Zo moet het topmanagement zich ervan bewust zijn dat het een belangrijke voorbeeldfunctie heeft. Dat geldt ook voor het gedrag van het management, dat zelf vanaf de start van de invoering in woord en daad dient te laten zien wat wenselijk is in de Lean-organisatie.
(...)
Het ontbreken van echt commitment van het topmanagement is een van de oorzaken van een stagnerende invoering van Lean. Bekende oorzaken van dit gebrek aan commitment zijn: (i)veranderingen in het topmanagement, (ii) het aanhangen van nieuwe hypes, en (iii) andere prioriteiten. ... [Écht] commitment van het topmanagement aan Lean blijkt uit het deelnemen aan de stuurgroep, uit het beschikbaar stellen van tijd en middelen aan de stuurgroep, uit de frequente aanwezigheid bij (verbeter)teams op de werkvloer (Gemba), uit het tijdig geven van feedback op operationele problemen en de daartoe voorgestelde verbeterideeën.
Volgens Van Assen zijn binnen het Lean leiderschap de volgende vijf 'instrumenten' cruciaal:
-
Mimiwo Kata Mukeru (luisteren): het (top)management moet echt bereid zijn te luisteren naar medewerkers en de wil hebben om van hen te leren.
-
Kanshin Sousa (interesse in de operatie): het (top)management heeft werkelijk interesse in de operationele problematiek.
-
Genchi Genbutsu (naar de werkplek): 'Genchi Genbutsu' is Japans voor 'teruggaan naar de bron' om de waarheden te vinden die nodig zijn om correcte beslissingen te nemen, en om consensus en doelstellingen te bereiken. Het idee is dat als de (top)manager het zelf niet direct gezien of ervaren heeft, zijn kennis per definitie incompleet is (vanwege de mogelijke ruis in het communicatiekanaal). Daarom moet het (top)management naar de werkvloer (terug naar de bron) om daar zelf te observeren en de problematiek te ervaren.
-
Nebari tsuyosa (volhardendheid): een bepaalde mate van volhardendheid is nodig om je niet zo snel uit het veld te laten slaan bij tegenslagen, die ongetwijfeld zullen komen doordat het gaat om een nieuwe manier van werken en ander gedrag waarbij diverse barrières overwonnen moeten worden om een continu naar perfectie strevende organisatie te bereiken.
-
Gyakusetsu (paradox): het management weet om te gaan met diverse managementparadoxen, waarbij een van belangrijkste paradoxen is de ogenschijnlijke tegenstelling tussen het sterk vasthouden aan de standard operating procedure (SOP; de best practice als norm) en het bieden van ruimte om te experimenteren om de huidige norm op de proef te stellen en zo verbeteringen te vinden: vrijheid in gebondenheid.
Bron: Handboek Lean management - aanpak, concepten en modellen voor het succesvol toepassen van Lean, Marcel van Assen
Laatst aangepast op dinsdag, 20 februari 2018 07:20
Resultaatverantwoordelijke teams volgens Marcel van Assen
Gepubliceerd in
Lean Six Sigma
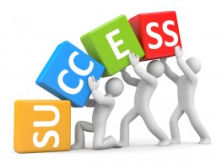
Marcel van Assen beschrijft in zijn boek Handboek Lean management het bij Philips ontwikkelde concept van de mini-company dat een uitwerking is van het continu verbeteren op de werkvloer. In het onderstaande volgt een fragment uit het boek waarin ik de term 'mini-company' vervang door de generieker inzetbare term 'resultaatverantwoordelijk team':

Een <resultaatverantwoordelijk team> is een semi-autonome productie-unit die over het algemeen een afgerond product aflevert en waarin de medewerkers de verantwoordelijkheid dragen voor de kwaliteit en het tijdig leveren van hun product. Het gaat erom dat de cel of groep zelf verantwoordelijk wordt voor zijn resultaten, en dat de medewerkers zich daar ook verantwoordelijk voor voelen. Ondersteunend hierbij is dat heel veel zaken visueel gemaakt worden, bijvoorbeeld via een wandbord met grafieken ... en duidelijke beknopte werkinstructies. Een <resultaatverantwoordelijk team> heeft de volgende kenmerken:
-
Een of meer wandborden met grafiekjes en afspraken.
-
Dag- en weekoverleg volgens een vaste structuur, gericht op het verbeteren.
-
Periodieke verbeterbijeenkomsten (op basis van verbeterborden).
-
Het team voelt zich 'zelfstandig' verantwoordelijk voor haar klanten.
-
Een plan met heldere afspraken hoe te verbeteren (verbeterroutines zoals de verbeter-Kata).
-
Een simpele beschrijving hoe men moet werken (gestandaardiseerd werk).
Een <resultaatverantwoordelijk team> heeft daarbij drie personen ('functionarissen') die de wekelijkse vergaderingen (keek-op-de-week) leiden en rapporten maken voor het bedrijfsmanagement. Een van hen is meer verantwoordelijk voor het organiseren en onderhouden van alle 'documentatie', zoals procesbeschrijvingen, standaardwerkmethoden en operating procedures. De andere functionaris is vooral verantwoordelijk voor het bijhouden van de prestatie-indicatoren en het geven van feedback over de prestatie van <team> door het verschaffen van visuele informatie. De derde functionaris houdt zich vooral bezig met het plannen en coördineren van het werk binnen het <team> en de logistieke afstemming met de afdeling.
Bron: Handboek Lean management - aanpak, concepten en modellen voor het succesvol toepassen van Lean, Marcel van Assen
Laatst aangepast op zaterdag, 14 juli 2018 15:21
|